Octavia Mk1
![]()
|
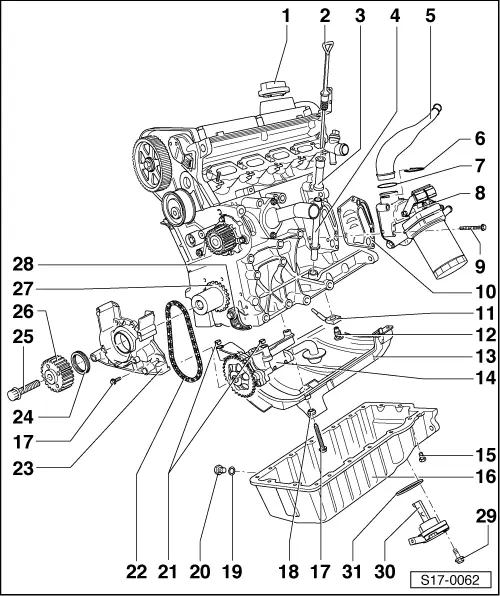
1 - | Plug |
q | Replace seal if damaged |
2 - | Dipstick |
q | oil level must not exceed max. marking! |
3 - | Filler funnel |
q | Remove for extracting oil |
4 - | Guide tube |
5 - | Connecting tube |
q | between oil filter holder and connecting hose to intake hose. |
6 - | Retaining clip |
q | check tightness |
7 - | O-ring |
q | replace if damaged |
8 - | Oil filter holder |
q | disassembling and assembling → Chapter |
9 - | 15 Nm + torque a further 90° (1/4 turn) |
10 - | Gasket with baffle plate |
q | replace |
q | Check fitting position |
11 - | Oil injection nozzle |
q | For piston cooling |
12 - | Pressure relief valve, 27 Nm |
q | opens at: 0,25 ... 0.32 MPa overpressure |
q | replace without sealant |
13 - | Baffle |
q | only mount when oil pump is fitted |
14 - | Oil pump with sprocket |
q | remove oil pan for removing and installing → Chapter |
q | disassembling and assembling → Chapter |
q | Testing oil pressure and oil pressure switch → Chapter |
15 - | 15 Nm |
q | loosen and tighten with hinged wrench and socket insert |
16 - | Oil pan |
q | removing and installing → Chapter |
17 - | 15 Nm |
18 - | Distance sleeve |
q | Check fitting position |
19 - | Gasket ring |
q | replace |
20 - | Oil drain plug, 40 Nm |
21 - | Fitting sleeve |
q | For centering oil pump/cylinder block |
22 - | Oil pump chain |
q | before removing mark running direction |
q | check for wear |
23 - | Front sealing flange |
q | must be positioned on dowel sleeves |
q | removing and installing → Chapter |
24 - | Gasket ring |
q | replace → Chapter |
25 - | Central screw |
q | replace |
q | 90 Nm + torque a further 90° (1/4 turn) |
q | to release and tighten use the counterholder -MP 1-310- |
q | when screwing on the counterholder place 2 washers between the timing belt gear and the counterholder |
26 - | Timing belt gear - crankshaft |
q | can be installed only in one position |
27 - | Sprocket |
q | for oil pump drive |
28 - | Chain tensioner with tensioning rail, 25 Nm |
q | Check fitting position |
q | Replace completely chain tensioner if spring is broken |
29 - | 10 Nm |
30 - | Oil level and temperature sender -G266- |
q | check → Current flow diagrams and Fitting locations |
31 - | Gasket |
q | replace if damaged |