Octavia Mk1

t | When installing new pinions or a new output shaft observe the technical data → Chapter. |
t | Replace both tapered-roller bearings together. |
t | Do not over-tension the circlips. Always replace damaged or over-tensioned circlips. |
t | If the clutch housing, output shaft (drive train) or tapered-roller bearing is replaced, it is necessary to adjust the output shaft → Chapter. |
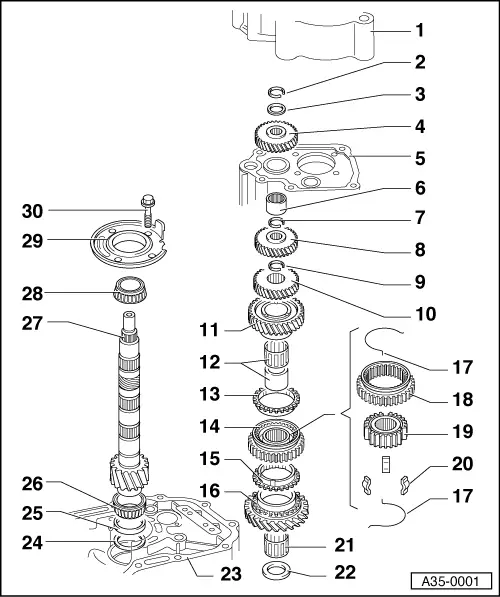
1 - | Cover for gearbox housing |
2 - | Circlip for 5th gear pinion |
3 - | Thrust washer |
4 - | 5th gear pinion |
q | removing and installing → Chapter |
5 - | Gearbox housing |
6 - | Needle bearing |
q | removing and installing → Chapter |
7 - | Circlip for 4th gear pinion |
8 - | 4th gear pinion |
q | Fitting position → Chapter |
9 - | Circlip for 3rd gear pinion |
q | Determining thickness again → Chapter |
10 - | 3rd gear pinion |
q | Fitting position → Chapter |
q | Set axial play → Chapter |
11 - | 2nd gear sliding gear |
12 - | Needle bearing for 2nd gear sliding gear |
q | Pull off inner ring → Chapter |
q | Press on inner ring → Chapter |
13 - | 2nd gear synchronizer ring |
q | check for wear → Fig. |
14 - | Sliding sleeve with 1st and 2nd gear synchronizer body |
q | Assembling sliding sleeve/synchronizer body → Fig. and → Fig. |
q | removing and installing → Chapter |
15 - | 1st gear synchronizer ring |
q | check for wear → Fig. |
q | Identification → Fig. |
16 - | 1st gear sliding gear |
17 - | Spring |
18 - | Sliding sleeve |
19 - | Synchronizer body |
20 - | Arresters |
q | 3 pieces |
21 - | Needle bearing |
q | for 1st gear |
22 - | Thrust washer |
q | Fitting position → Chapter |
23 - | Clutch housing |
24 - | Adjusting washer |
q | for output shaft |
q | Setting overview → Chapter |
25 - | Outer ring/tapered-roller bearing small |
q | removing → Fig. |
q | installing → Fig. |
26 - | Inner ring/tapered-roller bearing small |
q | pressing off → Fig. |
q | pressing on → Fig. |
27 - | Output shaft |
q | is paired with the gear pinion of the final drive, when replacing they must both be replaced |
q | adjust → Chapter |
28 - | Inner ring/tapered-roller bearing large |
q | pressing off → Fig. |
q | pressing on → Fig. |
29 - | Bearing support |
q | with outer ring/tapered-roller bearing large and stop for reverse gear |
q | Always replace outer ring together with tapered-roller bearing large and bearing support |
30 - | 25 Nm and torque a further 90° |
|
![]() |
Clearance -a- | Fitting dimension | Wear limit |
1st and 2nd gear | 1.1…1.7 mm | 0.5 mm |
|
![]() |
|
![]() |
|
![]() |
|
![]() |
|
![]() |
![]()
|
![]() |
![]()
|
![]() |
|
![]() |