Octavia Mk1

t | When installing new pinions or a new output shaft observe the technical data → Chapter. |
t | If the output shaft or tapered-roller bearing is replaced, it is necessary to adjust the output shaft → Chapter. |
t | Both tapered-roller bearings are replaced together. |
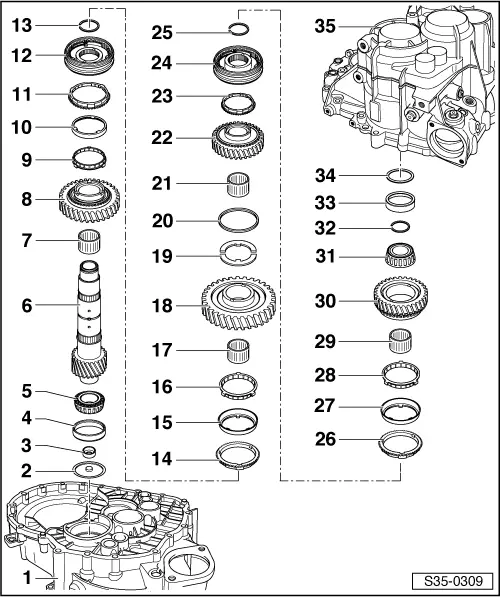
1 - | Clutch housing |
2 - | Oil deflecting washer |
3 - | Curved washer |
q | removing → Fig. |
q | installing → Fig. |
q | replace after disassembly → Electronic Catalogue of Original Parts |
4 - | Outer ring/tapered-roller bearing |
q | removing → Fig. |
q | installing → Fig. |
5 - | Inner ring/tapered-roller bearing |
q | pressing off → Fig. |
q | pressing on → Fig. |
6 - | Output shaft |
q | 1st to 4th gear |
q | adjust → Chapter |
7 - | Needle bearing |
q | for 2nd gear |
8 - | 2nd gear sliding gear |
9 - | Synchronizer ring |
q | (Inner ring for 2nd gear) |
q | check for wear → Fig. |
q | Check pegs for traces of wear |
q | Fitting position → Fig. |
10 - | Outer ring for 2nd gear |
q | position on the synchronizer ring -Pos. 9- |
q | replace if there are any traces of scoring or friction |
q | Fitting position → Fig. |
11 - | 2nd gear synchronizer ring |
q | check for wear → Fig. |
q | Fitting position → Fig. |
12 - | Sliding sleeve with 1st and 2nd gear synchronizer body |
q | after removing the circlip -Pos. 13- press off with the 2nd gear sliding gear → Fig. |
q | disassembling → Fig. |
q | Assembling sliding sleeve/synchronizer body → Fig. and → Fig. |
q | Fitting position → Fig. |
q | pressing on → Fig. |
13 - | Circlip |
14 - | 1st gear synchronizer ring |
q | check for wear → Fig. |
q | insert in such a way that the recesses lock into the arresters of the sliding sleeve/synchronizer body Pos. 12 |
15 - | Outer ring for 1st gear |
q | insert into synchronizer ring Pos. 14, fitting position → Fig. |
q | replace if there are any traces of scoring or friction |
16 - | Synchronizer ring |
q | (Inner ring for 1st gear) |
q | check for wear → Fig. |
q | Check pegs for traces of wear |
q | Fitting position → Fig. |
17 - | Needle bearing |
q | for 1st gear |
18 - | 1st gear sliding gear |
q | Fitting position → Fig. |
19 - | Thrust washers |
q | for 1st and 4th gear |
q | 2 pieces |
q | Insert peg of thrust washer into the hole of the output shaft |
20 - | Washer |
q | holds the thrust washers pos. 19 in the correct position on the output shaft |
21 - | Needle bearing |
q | for 4th gear |
22 - | 4th gear sliding gear |
23 - | 4th gear synchronizer ring |
q | check for wear → Fig. |
24 - | Sliding sleeve with 3rd and 4th gear synchronizer body |
q | after removing the circlip -Pos. 25- remove with the 4th gear sliding gear → Fig. |
q | disassembling → Fig. |
q | Fitting position sliding sleeve/synchronizer body → Fig. |
q | Assembling sliding sleeve/synchronizer body → Fig. and → Fig. |
q | pressing on → Fig. |
25 - | Circlip |
26 - | 3rd gear synchronizer ring |
q | check for wear → Fig. |
27 - | Outer ring for 3rd gear |
q | fit into synchronizer ring -Pos. 26-, fitting position → Fig. |
q | replace if there are any traces of scoring or friction |
28 - | Synchronizer ring |
q | (Inner ring for 3rd gear) |
q | check for wear → Fig. |
q | Check pegs for traces of wear |
q | Fitting position → Fig. |
29 - | Needle bearing |
q | for 3rd gear |
30 - | 3rd gear sliding gear |
q | Fitting position → Fig. |
31 - | Inner ring/tapered-roller bearing |
q | remove → Fig. |
q | pressing on → Fig. |
32 - | Circlip |
q | determine the thickness again when replacing the tapered-roller bearing Pos. 31 and the output shaft Pos. 6 → Fig. |
33 - | Outer ring/tapered-roller bearing |
q | removing → Fig. |
q | installing → Fig. |
34 - | Adjusting washer |
q | Determine thickness → Chapter |
35 - | Gearbox housing |
|
![]() |
![]()
|
![]() |
|
![]() |
|
![]() |
|
![]() |
|
![]() |
|
![]() |
|
![]() |
|
![]() |
|
![]() |
Clearance -a- | Fitting dimension | Wear limit |
1st, 2nd and 3rd gear | 0.75…1.25 mm | 0.3 mm |
|
![]() |
Clearance -a- | Fitting dimension | Wear limit |
1st, 2nd and 3rd gear | 1.2…1.8 mm | 0.5 mm |
|
![]() |
|
![]() |
|
![]() |
|
![]() |
|
![]() |
|
![]() |
|
![]() |
|
![]() |
|
![]() |
|
![]() |
|
![]() |
Clearance -a- | Fitting dimension | Wear limit |
4th gear | 1.0…1.7 mm | 0.5 mm |
|
![]() |
|
![]() |
Thickness (mm) | ||
1,79 | 1,89 | 1,98 |
1,83 | 1,92 | |
1,86 | 1,95 |
|
|
![]() |
|
![]() |