Roomster

t | Before installing, heat the inner ring/tapered-roller bearing with the hot-air blower -V.A.G 1416- to 100°C. |
t | Replace both tapered-roller bearings together. |
t | When replacing the tapered-roller bearing of the differential gear housing, gearbox housing and clutch housing adjust the differential gear → Chapter. |
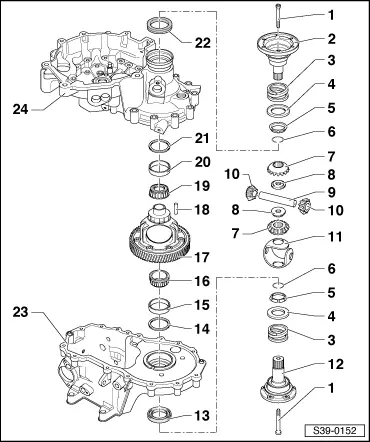
1 - | Conical screw, 25 Nm |
q | screw into threaded piece -Pos. 8- |
2 - | Right flange shaft |
q | do not interchange, the left and right flange shafts are different |
3 - | Pressure spring for flange shaft |
q | fitted behind flange shaft |
4 - | Thrust washer |
q | Fitting position: Collar towards pressure spring |
5 - | Conical ring |
q | Fitting position: Cone towards differential gear housing |
6 - | Circlip |
q | holds the conical ring, stop disc and pressure spring in position when the flange shaft is removed |
7 - | Large differential bevel gear |
q | installing → Fig. |
8 - | Threaded part |
q | installing → Fig. |
9 - | Differential bevel gear shaft |
q | when removing, the tensioning sleeve -Pos. 18- is cut out → Fig. |
q | installing → Fig. |
10 - | Small differential bevel gear |
q | installing → Fig. |
11 - | Stop disc compound |
q | when installing moisten with gearbox oil |
q | on certain gearboxes the stop disc compound was provided with a land → Fig. |
12 - | Flange shaft left |
q | with dust guard |
q | do not interchange, the left and right flange shafts are different |
13 - | Sealing ring |
q | for left flange shaft |
q | diameter of left and right differ |
q | replace with installed gearbox → Chapter |
14 - | Adjusting washer S1 |
q | for differential gear |
q | always 1 mm thick |
q | on gearboxes made out of aluminium as of production date 12.06 the adjusting washer S1 for outer ring/tapered-roller bearing is not fitted → Chapter |
q | Bearing pedestal for outer ring/tapered-roller bearing is adapted |
q | Assignment → Electronic Catalogue of Original Parts |
15 - | Outer ring/tapered-roller bearing |
q | removing → Fig. |
q | installing → Fig. |
16 - | Inner ring/tapered-roller bearing |
q | remove → Fig. |
q | pressing on → Fig. |
17 - | Differential gear housing |
q | with riveted pinion for final drive |
q | is paired with the output shaft, replace together |
18 - | Tensioning sleeve |
q | to secure the differential bevel gear shaft |
q | is cut when removing → Fig. |
q | installing → Fig. |
19 - | Inner ring/tapered-roller bearing |
q | remove → Fig. |
q | pressing on → Fig. |
20 - | Outer ring/tapered-roller bearing |
q | pressing out → Fig. |
q | installing → Fig. |
21 - | Adjusting washer S2 |
q | for differential gear |
q | Determine thickness → Chapter |
22 - | Sealing ring |
q | for right flange shaft |
q | diameter of left and right differ |
q | replace with installed gearbox → Chapter |
23 - | Gearbox housing |
q | is made out of aluminium or magnesium → Chapter |
q | on gearboxes made out of aluminium as of production date 12.06 the adjusting washer S1-Pos. 14- for outer ring/tapered-roller bearing is not fitted → Chapter |
q | Bearing pedestal for outer ring/tapered-roller bearing is adapted |
q | Assignment → Electronic Catalogue of Original Parts |
q | repairing → Chapter |
24 - | Clutch housing |
q | is made out of aluminium or magnesium → Chapter |
q | Assignment → Electronic Catalogue of Original Parts |
q | repairing → Chapter |
|
![]() |
![]()
|
![]() |
|
![]() |
|
![]() |
|
![]() |
|
![]() |
|
![]() |
|
![]() |
|
![]() |
|
![]() |
|
![]() |