Roomster
![]()
![]()
|
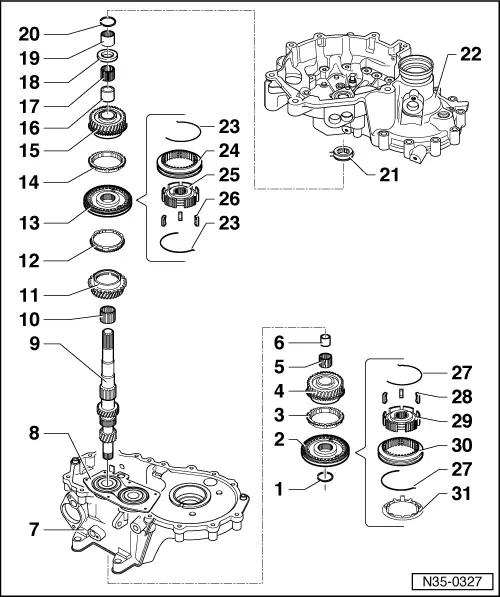
1 - | Circlip |
q | always replace → Electronic Catalogue of Original Parts |
q | Determine thickness → Chapter |
2 - | Sliding sleeve with 5th gear synchronizer body |
q | removing and installing → Chapter |
q | disassembling → Fig. |
q | Assembling sliding sleeve/5th gear synchronizer body → Fig. and → Fig. |
q | on gearboxes as of production date 06.09, the springs -Pos. 27- are changed |
3 - | 5th gear synchronizer ring |
q | check for wear → Fig. |
4 - | 5th gear sliding gear |
5 - | Needle bearing |
q | 5th gear |
q | replace together with -Pos. 6- |
q | Assignment → Electronic Catalogue of Original Parts |
6 - | Bushing |
q | for 5th gear needle bearing |
q | replace together with -Pos. 5- |
q | press off with bearing support for grooved ball bearing → Fig. |
q | pressing on → Fig. |
q | Assignment → Electronic Catalogue of Original Parts |
7 - | Gearbox housing |
8 - | Bearing support for grooved ball bearing |
q | Always replace grooved ball bearing together with the bearing support |
q | If the bearing support is released from the gearbox housing, it must always be replaced |
q | pressing off → Fig. |
q | pressing on → Fig. |
9 - | Drive shaft |
10 - | Needle bearing |
q | for 3rd gear |
q | Assignment → Electronic Catalogue of Original Parts |
11 - | 3rd gear sliding gear |
12 - | 3rd gear synchronizer ring |
q | on gearboxes as of production date 06.09, the synchronizer ring for 3rd and 4th gear is changed → Electronic Catalogue of Original Parts |
q | check for wear → Fig. |
13 - | Sliding sleeve with 3rd and 4th gear synchronizer body |
q | press off with 3rd gear sliding gear → Fig. |
q | disassembling → Fig. |
q | Fitting position sliding sleeve/synchronizer body → Fig. |
q | Assemble sliding sleeve/synchronizer body → Fig. and → Fig. |
q | pressing on → Fig. |
q | on gearboxes as of production date 06.09, the springs (-Pos. 23-) are changed |
14 - | 4th gear synchronizer ring |
q | on gearboxes as of production date 06.09, the synchronizer ring for 3rd and 4th gear is changed → Electronic Catalogue of Original Parts |
q | check for wear → Fig. |
15 - | 4th gear sliding gear |
16 - | Bushing |
q | for 4th gear needle bearing |
q | replace together with -Pos. 17- |
q | removing → Fig. |
q | installing → Fig. |
q | Assignment → Electronic Catalogue of Original Parts |
17 - | Needle bearing |
q | for 4th gear |
q | replace together with -Pos. 16- |
q | Assignment → Electronic Catalogue of Original Parts |
18 - | Thrust washer |
19 - | Inner ring |
q | for cylindrical-roller bearing |
q | pull off with 4th gear sliding gear → Fig. |
q | pressing on → Fig. |
20 - | Circlip |
q | always replace → Electronic Catalogue of Original Parts |
q | Determine thickness → Fig. |
21 - | Cylindrical-roller bearing |
q | with circlip |
q | removing → Fig. |
q | pressing on → Fig. |
q | Fitting position: the circlip in the bearing points towards the drive shaft |
22 - | Clutch housing |
q | repairing → Chapter |
23 - | Spring |
q | on gearboxes as of production date 06.09, the springs of the sliding sleeve with synchronizer body for 3rd, 4th and 5th gear are changed (the springs are longer) |
q | Fitting position → Fig. |
24 - | Sliding sleeve 3rd and 4th gear |
25 - | 3rd and 4th gear synchronizer body |
26 - | Arresters for synchronizer body |
q | (3 pieces) |
27 - | Spring |
q | on gearboxes as of production date 06.09, the springs of the sliding sleeve with synchronizer body for 3rd, 4th and 5th gear are changed (the springs are longer) |
q | Fitting position → Fig. |
28 - | Arresters for synchronizer body |
q | (3 pieces) |
29 - | 5th gear synchronizer body |
30 - | 5th gear sliding sleeve |
31 - | Supporting ring |
q | prevents the arresters from wandering |
q | removing → Fig. |
q | installing → Fig. |
|
![]() |
![]()
|
![]() |
|
![]() |
|
![]() |
|
![]() |
|
![]() |
|
![]() |
|
![]() |
|
![]() |
3rd, 4th and 5th gear | Fitting dimension | Wear limit |
Clearance -a- | 1.1 to 1.7 mm | 0.5 mm |
|
![]() |
|
![]() |
![]()
|
![]() |
Measured value (mm) | Circlip thickness (mm) | Axial play (mm) |
0,05…0,14 | 2,0 | 0,05…0,15 |
0,15…0,24 | 2,1 | 0,05…0,15 |
0,25…0,34 | 2,2 | 0,05…0,15 |
0,35…0,44 | 2,3 | 0,05…0,15 |
0,45…0,51 | 2,4 | 0,05…0,10 |
![]() |
|
![]() |
|
![]() |
|
![]() |
|
![]() |
|
![]() |
|
![]() |
|
![]() |