Leon Mk2
Repairing drive shaft from model year 2001 |
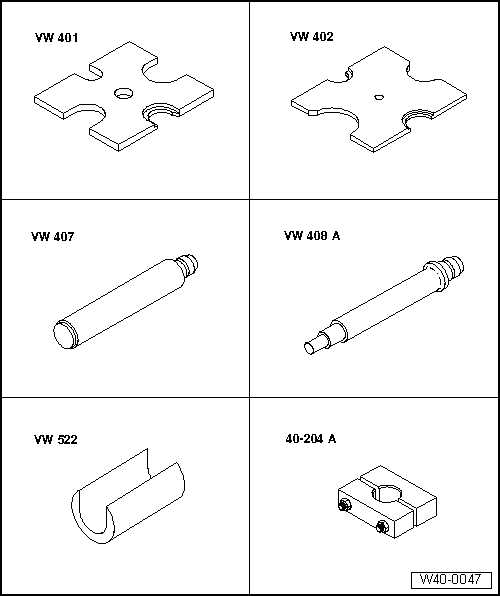
Special tools and workshop equipment required |
t | Press plate -VW 401- |
t | Press plate -VW 402- |
t | Press tool -VW 407- |
t | Press tool -VW 408 A- |
t | Support sleeve -VW 522- |
t | Tensioner -40-204 A- |
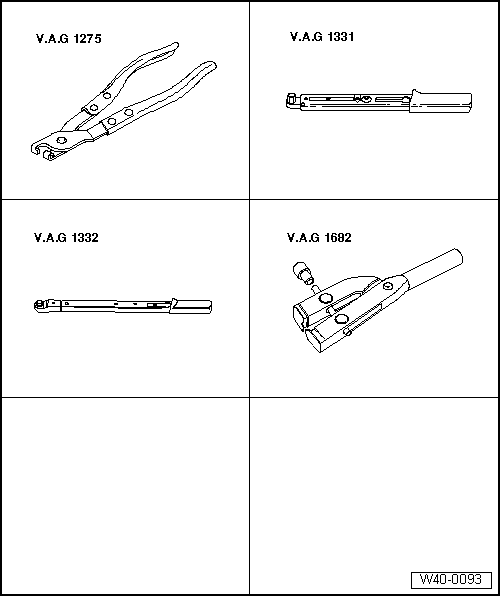
t | Pliers -V.A.G 1275- |
t | Torque wrench -V.A.G 1331- |
t | Torque wrench -V.A.G 1332- |
t | Pliers -V.A.G 1682- |
|
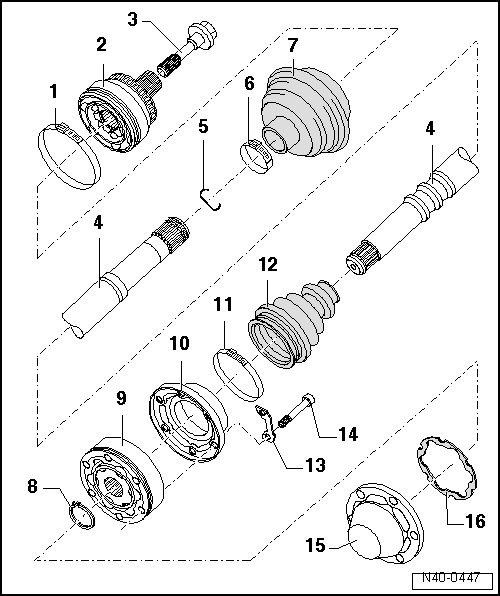
1 - | Clamp-type clip |
q | Renew. |
q | Tensioning → Fig.. |
2 - | Outer constant velocity joint |
q | Renew only complete. |
q | Driving off → Fig.. |
q | Checking → Chapter. |
q | Installing: drive onto shaft with plastic hammer until compressed circlip seats. |
q | Greasing → . |
3 - | Hexagon bolt |
q | 150 Nm and turn 90° further. |
q | The vehicle must be standing on the ground when loosening/tightening. |
q | Renew each time after removing. |
4 - | Drive shaft |
5 - | Circlip |
q | Renew. |
q | Insert in shaft groove. |
6 - | Clamp-type clip |
q | Renew. |
q | Tensioning → Fig.. |
7 - | Bellows for outer constant velocity joint |
q | Material: Hytrel (Polyelastomer). |
q | No breather hole. |
q | Check for tears and chafing, renew if necessary. |
8 - | Circlip |
q | Renew. |
9 - | Inner constant velocity joint |
q | Renew only complete. |
q | Pressing off → Fig.. |
q | Checking → Chapter. |
q | Pressing on → Fig.. |
q | Adhesive surface must be free of oil and grease. |
q | Greasing → . |
q | Remove and install with long nosed pliers. |
10 - | Cap |
q | Drive off with a drift. |
q | Before fitting on constant velocity joint, coat sealing surface with D-3. |
q | Adhesive surface must be free of oil and grease. |
11 - | Clamp-type clip |
q | Renew. |
q | Tensioning → Fig.. |
12 - | Bellows for inner constant velocity joint |
q | With vent hole |
q | Check for tears and chafing, renew if necessary. |
q | Clean drive shaft thoroughly before installing new drive shaft bellows. |
q | Lightly grease the drive shaft before installing the bellows. |
13 - | Locking plate |
14 - | Multi-point socket head bolt |
q | Tighten using diagonal sequence to 10 Nm. |
q | Tighten to 70 Nm. |
q | Renew each time after removing. |
15 - | Cover |
q | Drive off with a drift → Fig.. |
q | Adhesive surface must be free of oil and grease. |
q | Before fitting on constant velocity joint, coat sealing surface with D-3. |
16 - | Seal |
q | Renew. Pull off protective foil and stick onto joint. |
![]()
|
![]() |
|
![]() |
|
![]() |
|
![]() |
|
![]() |
![]()
|
![]() |