Freelander System Description and Operation
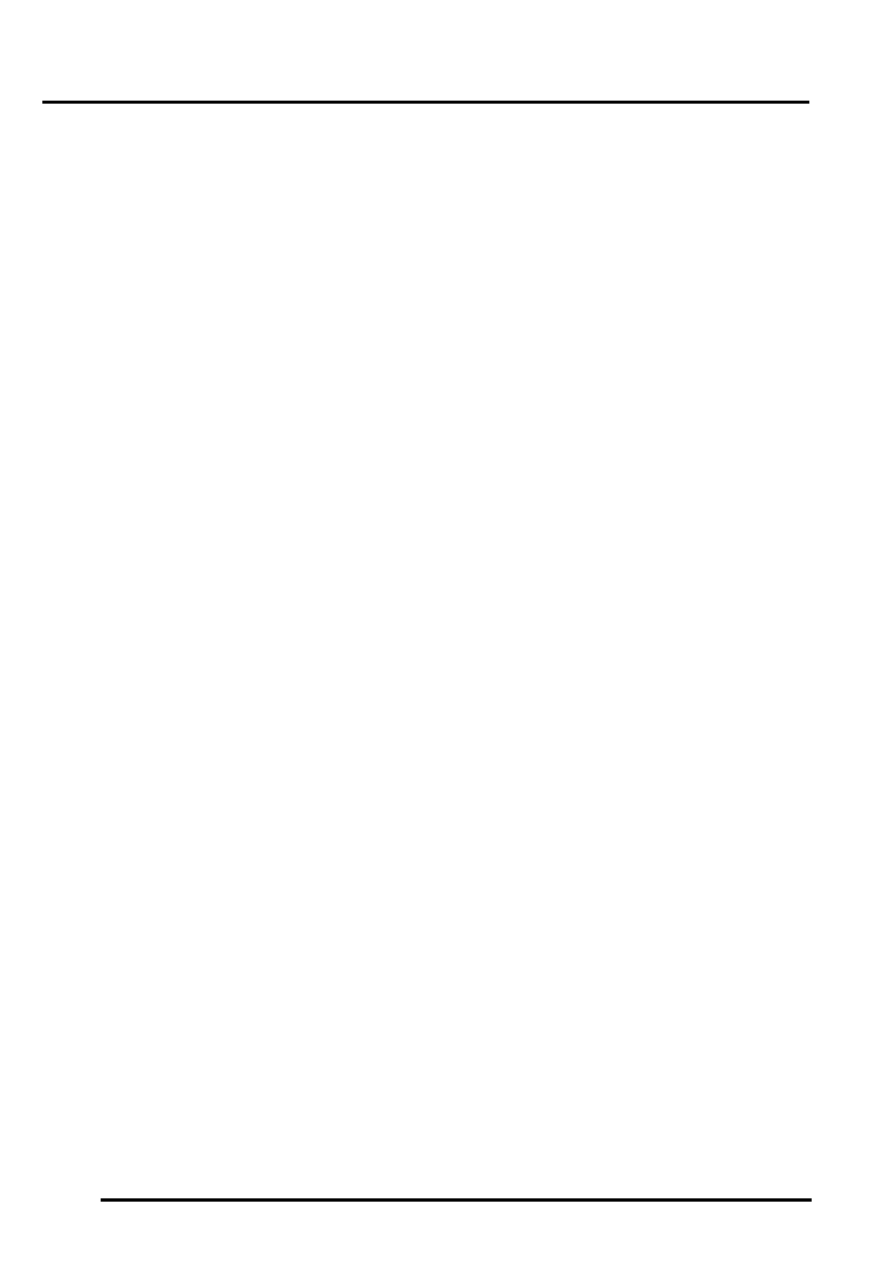
BRAKES
70-8
DESCRIPTION AND OPERATION
Brake Servo Assembly
The brake servo assembly provides power assistance to reduce the pedal load when braking.
The assembly is attached to the front of the pedal box and comprises a circular housing containing a diaphragm, push
rods, valve and filter. A push rod at the rear of the housing is connected to the brake pedal. The vacuum line is
connected to a port in the front face of the housing.
With the brake pedal released and the engine running, vacuum pressure is present on both sides of the diaphragm.
When the brake pedal is pressed, the rear push rod moves forward and opens the valve to allow atmospheric pressure
through the filter into the pedal side of the diaphragm. The pressure differential acting on the diaphragm increases the
pressure being applied by the brake pedal, which is transmitted to the master cylinder via the forward push rod.
If the servo fails, the hydraulic system will still function but will require greater pedal effort due to the lack of vacuum
assistance.
Vacuum Enhancer System
Vehicles from 2003 model year – The vacuum enhancer solenoid valve is no longer fitted to vehicles from 2003
model year onwards. On these vehicles the solenoid valve is removed, but the venturi valve and associated piping is
retained. On this system the vacuum enhancement is still required, but due to the deletion of the air assist injectors,
the vacuum enhancement can be permanently operated.
The vacuum enhancer system increases the relatively low vacuum available from the inlet manifold to increase
braking assistance. The system consists of a venturi valve, a solenoid valve and associated pipes.
The venturi valve is installed in the vacuum pipe between the brake servo and the inlet manifold. An air feed pipe,
from the intake duct upstream of the throttle body via the solenoid valve, is also connected to the venturi valve. Internal
ducts in the venturi valve connect the brake servo and air feed ports to the inlet manifold port. The duct connecting
the air feed port to the inlet manifold port incorporates the venturi. A check valve, integrated into the brake servo port,
prevents the reverse flow of air and fuel vapour to the brake servo.
The solenoid valve controls the air feed to the venturi valve. Operation of the solenoid valve is controlled by the ECM.
To improve engine idle speed refinement, when the gearbox lever is in Park or Neutral, the solenoid valve is closed
and the brake servo senses the vacuum in the inlet manifold via the venturi valve. When the gearbox lever is selected
to positions other than Park or Neutral, the ECM energises the solenoid valve and air from the upstream side of the
throttle body is fed to the venturi valve. The air flows through the venturi valve into the inlet manifold. As the air flows
through the venturi in the venturi valve, it increases in velocity and decreases in pressure, resulting in an increase in
the vacuum sensed by the brake servo. Depending on ambient conditions and engine speed, the vacuum enhancer
system increases inlet manifold vacuum by a maximum of approximately 40%.
Master Cylinder Assembly
The master cylinder assembly produces hydraulic pressure to operate the brakes when the brake pedal is pressed.
The assembly is attached to the front of the brake servo assembly, and comprises a cylinder containing two pistons
in tandem. The rear piston produces pressure for the primary circuit and the front piston produces pressure for the
secondary circuit.
The brake fluid reservoir is located either on top of the master cylinder assembly (LH drive vehicles) or above the
master cylinder on a bracket on the bulkhead (RH drive vehicles). The reservoir is internally divided to provide an
independent supply of fluid to each brake circuit, and so prevent a single fluid leak from disabling both primary and
secondary brake circuits.
Should a failure occur in one circuit, the remaining circuit will still operate effectively, although brake pedal travel and
vehicle braking distances will increase. If the fluid level in the reservoir is too low, the brake fluid level switch in the
reservoir filler cap breaks a contact to the ABS ECU, which sends a CAN message to illuminate the brake warning
lamp in the instrument pack.