Leon Mk1
Primary shaft: dismounting and assembly |
t | If new pinions have to be fitted, consult the Identification Initials section, group assignment, reductions, filling capacities → Chapter. |
t | The primary shaft must always be adjusted when any component affecting the position of the tapered bearing bushes has been replaced → Chapter. |
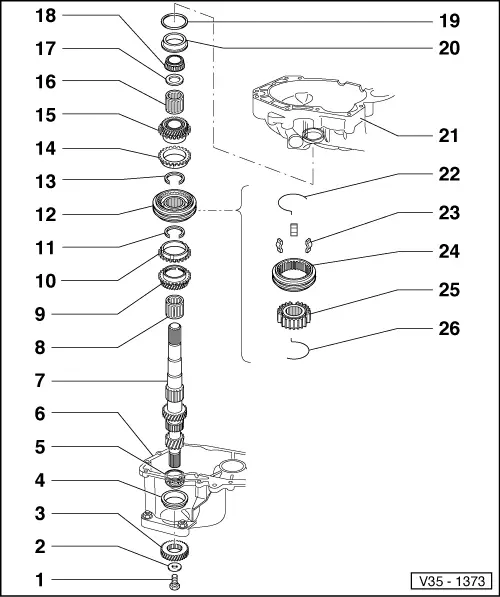
1 - | Securing screw for the 5th gear pinion, 40 Nm |
2 - | Disc spring |
q | The concave side must face the 5th gear pinion. |
3 - | 5th gear pinion |
q | Dismounting and assembly → Anchor |
4 - | Outer track, tapered roller bearing |
q | Dismounting → Fig. |
q | Assembly → Fig. |
5 - | Tapered roller bearing |
q | Dismounting → Fig. |
q | Assembly → Fig. |
6 - | Gearbox casing |
7 - | Primary shaft |
q | If being replaced, the primary shaft should be adjusted. |
q | Adjustment of the primary shaft → Chapter |
8 - | Needle bearing |
q | Oil well before assembling. |
9 - | 3rd gear pinion |
q | Dismounting → Fig. |
q | Assembly → Fig. |
q | Assemble together with the sliding sleeve and the synchroniser bush for 3rd and 4th gears. |
10 - | Synchroniser bush 3rd gear |
q | Checking for wear → Fig. |
11 - | Guard ring |
q | Detachment → Fig. |
q | Attachment → Fig. |
12 - | Synchroniser unit for 3rd and 4th gears |
q | The parts come in pairs. |
q | Detachment → Fig. |
q | Assembly → Fig. and → Fig. |
q | Assembly on the primary shaft → Fig. |
13 - | Guard ring |
q | Detachment → Fig. |
q | Attachment → Fig. |
14 - | 4th gear synchroniser bush |
q | Checking for wear → Fig. |
15 - | 4th gear pinion |
16 - | Needle bearing |
q | Impregnate with gear oil before assembling |
17 - | Retainer washer |
18 - | Tapered roller bearing |
q | Can be detached and assembled without using tools |
19 - | Adjusting washer |
q | For the primary shaft |
q | Calculate the thickness → Chapter |
20 - | Outer track, tapered roller bearing |
q | Detachment → Fig. |
q | Assembly → Fig. |
21 - | Clutch casing |
22 - | Spring |
q | Assembly position → Fig. |
23 - | Cotters |
24 - | Sliding sleeve |
25 - | Synchroniser bush |
q | Bush identification → Fig. |
26 - | Spring |
q | Assembly position → Fig. |
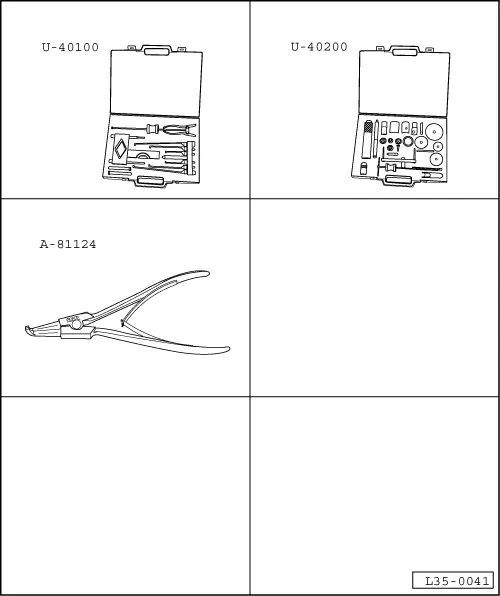
Special tools and workshop equipment required |
t | Replacement parts extractors case -U-40100- |
t | Replacement parts repair case -U-40200- |
t | Pliers for opening spring rings -A-81124- |
t | Electrical blower -SAT 1416- |
t | Universal tester stand -T20020- |
![]()
|
![]() |
|
![]() |
|
![]() |
|
![]() |
|
![]() |
|
![]() |
|
![]() |
![]()
|
![]() |
|
![]() |
Synchroniser ring | Measurement “a” in new synchroniser | Limit of wear |
3rd and 4th gear | 1,1…1,7 mm | 0,5 mm |
|
![]() |
|
![]() |
|
![]() |