Leon Mk1
|
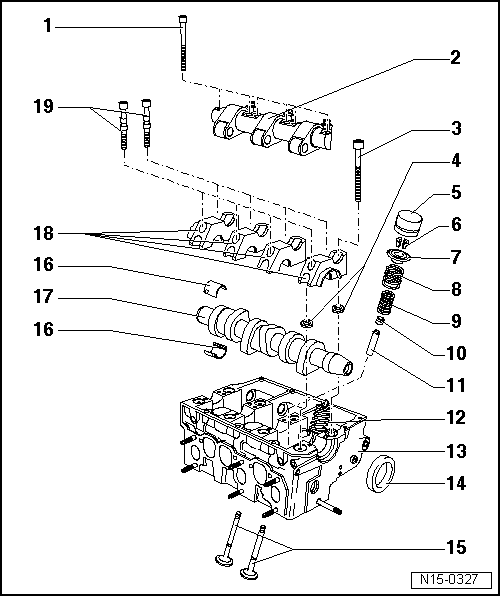
1 - | 20 Nm + 90° (1/4 turn) |
q | Replace |
q | Observe sequence when loosening and tightening → Chapter. |
2 - | Rocker axle |
3 - | Cylinder head bolt |
q | Replace |
q | Observe sequence when loosening and tightening → Chapter. |
q | Prior to installation, insert washers → Item in cylinder head |
4 - | Plate |
q | For cylinder head bolts |
5 - | Hydraulic followers: |
q | Do not mix them up |
q | With hydraulic valve clearance compensation. |
q | Set down with cam bearing surface facing downwards. |
q | Before installing, check camshaft axial clearance → Fig.. |
q | Lubricate contact surface |
q | Before separation, extract the half bearings from the camshaft |
6 - | Valve half-cones |
7 - | Valve plate spring |
8 - | Exterior valve spring |
q | Removing and fitting with the cylinder head removed using the valve installation tool -T20034/1-. Cylinder head fitted → Chapter |
9 - | Interior valve spring |
q | Removing and fitting with the cylinder head removed using the valve installation tool -T20034/1-. Cylinder head fitted → Chapter |
10 - | Valve stem seal |
q | replace → Chapter |
11 - | Valve guide |
q | Checking → Chapter |
q | If the wear limit is still exceeded, replace the cylinder head |
12 - | Injector pump |
q | removing and fitting → Chapter |
13 - | Cylinder head |
q | See note → Chapter |
q | Reworking valve seats → Chapter. |
14 - | Oil seal |
q | Do not additionally oil or grease the oil seal sealing lip. |
q | Before fitting, clean the remains of oil on the crankshaft journal using a clean cloth. |
q | For fitting, cover the camshaft cone groove (for ex. With cellophane) |
q | removing and fitting → Chapter |
15 - | Valves: |
q | Valve dimensions → Fig. |
16 - | Bearing cap |
q | Do not interchange used bearing shells (mark). |
q | Ensure the correct seating in the allotment |
17 - | Camshaft: |
q | check the axial play → Fig. |
q | removing and fitting → Chapter |
q | Check the radial play using a Plastigage: Wear limit: 0.11 mm |
q | Radial clearance: Max. 0.01 mm |
q | Identification and distribution time → Fig. |
18 - | Bearing cap |
q | Fitting order → Chapter |
q | The bearing cap 4 is identified as bearing cap 5. |
q | Seal contact surfaces of bearing caps 1 and 4 for installation → Spare parts catalogue → Fig. |
19 - | 8 Nm + 90° (1/4 turn) |
q | Replace |
|
|
![]() |
|
![]() |
![]()
|
![]() |
![]()
|
![]() |
Dim. | Inlet valve | Outlet valve | |
Ø a | mm | 35,95 | 31,45 |
Ø b | mm | 6,980 | 6,956 |
c | mm | 89,95 | 89,95 |
α | ∠° | 45 | 45 |
Inlet opens at TDC | 15,8° |
Inlet closed at BDC | 25,3° |
Exhaust opens before BDC | 28,2° |
Exhaust closes before TDC | 18,7° |