Leon Mk1
|
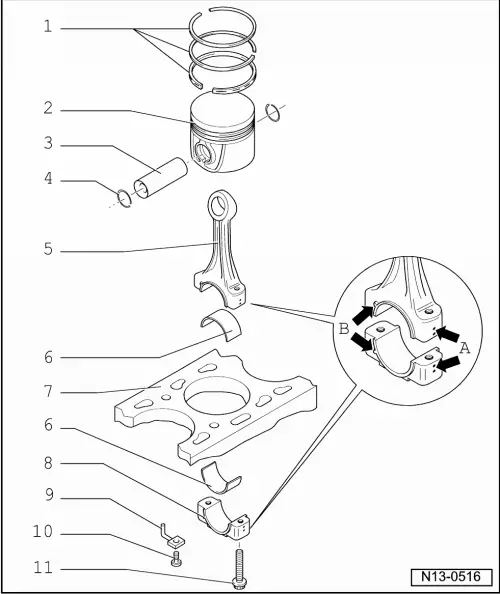
1 - | Piston rings |
q | Offset gaps by 120° |
q | Use piston ring pliers to remove and install |
q | The mark „TOP“ must face towards piston crown |
q | Piston ring ends: check → Fig. |
q | Groove clearance: check → Fig. |
2 - | Piston |
q | Mark installation position and cylinder number. |
q | Arrow on piston crown points to pulley end |
q | Install with piston ring compressor |
q | If the piston is scratched, replace it |
q | Position of the piston in TDC: verification → Chapter |
3 - | Piston pin |
q | If difficult to move, heat piston to 60 °C |
q | Removing and installing with the piston rod installation tool -T20019- |
4 - | Retainer washer |
5 - | Conrod |
q | Replace only in sets |
q | Mark cylinder allocation -A- with coloured pen. |
q | Fitting position: The marks -B- should point towards the pulley |
6 - | Bearing cap |
q | Installation position → Fig. |
q | Note design: Upper half bearing shell (to piston) made from high resistance material. Identification: Black line on the sliding surface in the cutting area |
q | Do not interchange used bearing shells. |
q | Axial play, wear limit: 0.37 mm |
q | Check the radial play using a Plastigage: Wear limit: 0.08 mm when measuring the radial play, do not rotate the crankshaft |
7 - | cylinder block |
q | Checking cylinder bore → Fig. |
q | Piston and cylinder dimensions → Chapter |
8 - | Conrod bearing cap |
q | Note fitting position: |
9 - | Oil spray jet |
q | For piston cooling |
q | Observe the fitting position: Turn the oil injection nozzle anticlockwise up until the end of the cylinder block and fix in this position. |
10 - | Hollow bolt with valve, -25 Nm |
q | 4x |
q | Fit without using sealant |
11 - | 30 Nm + 90° (1/4 turn) |
q | Renew |
q | Oil threads and contact surface. |
q | Tightening the bolts equally with 5 Nm |
q | To measure the radial play use a used bolt |
|
![]() |
Piston ring Dimensions in mm | When new | Wear limit |
1. compression ring | 0,20...0,40 | 1,0 |
2nd compression ring | 0,20...0,40 | 1,0 |
Oil scraping ring | 0,25...0,50 | 1,0 |
|
![]() |
Piston ring Dimensions in mm | When new | Wear limit |
1. compression ring | 0,06...0,09 | 0,25 |
2nd compression ring | 0,05...0,08 | 0,25 |
Oil scraping ring | 0,03...0,06 | 0,15 |
|
![]() |