Leon Mk1
![]() |
|
![]() |
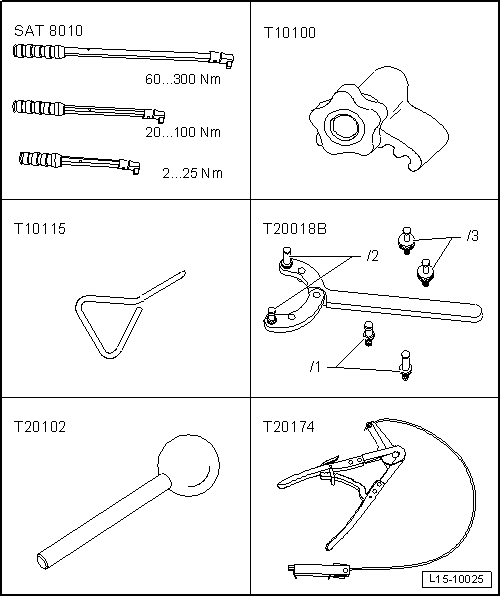
Special tools and workshop equipment required |
t | Torque wrench -SAT 8010-, see equivalent → Anchor. |
t | Hose clamp -T10100-, see equivalent → Anchor |
t | Hose clamp -T10115-, see equivalent → Anchor |
t | Hose clamp -T20018B-, see equivalent → Anchor |
t | Hose clamp -T20102-, see equivalent → Anchor |
t | counterhold -T20174-, see equivalent → Anchor |
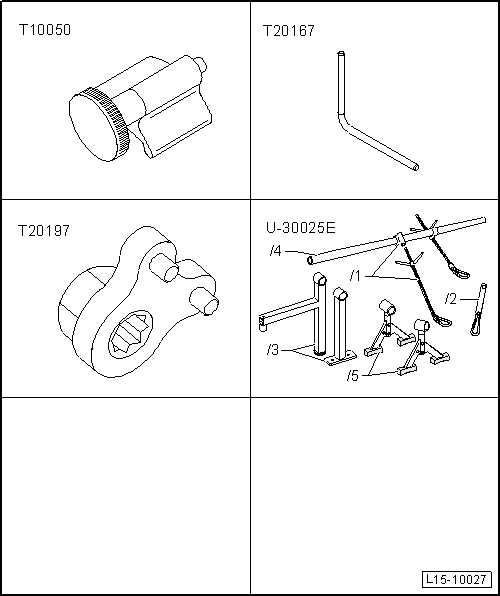
t | Hose clamp -T10050-, see equivalent → Anchor |
t | Hose clamp -T20167-, see equivalent → Anchor |
t | Turning tool -T20197-, see equivalent → Anchor |
t | Socket -U-30025E-, see equivalent → Anchor |
|
|
![]() |
|
![]() |
|
![]() |
|
![]() |
|
![]() |
|
![]() |
|
![]() |
![]() |
![]() |
|
![]() |
|
![]() |
|
![]() |
|
![]() |
|
![]() |
|
![]() |
|
![]() |
![]()
|
![]() |
![]()
|
![]() |
|
![]() |
|
![]() |
|
![]() |
|
![]() |
|
![]() |
|
![]() |
|
![]() |
![]()
|
![]() |
|
![]() |
![]()
|
![]() |
|
![]() |
![]() |
![]() |
![]()
|
![]() |
![]() |
![]() |
![]()
|
![]() |
|
![]() |
|
![]() |
|
![]() |
|
![]() |
|
![]() |
|
![]() |
![]()
![]() |
![]() |
|
![]() |
|
![]() |
|
![]() |
|
![]() |
|
![]() |
|
![]() |
![]()
|
![]() |
|
![]() |
Component | Nm | |
Notched belt tensioning roller to cylinder head | 20 + 45° → Note | |
Camshaft pinion to bin | 25 | |
Bottom section of notched belt guard to cylinder block | 10 → Note | |
Centre section of notched belt guard to cylinder block | 10 → Note | |
Vibration damper to the crankshaft wheel | 10 + 90° → Note → Note | |
Engine mount to the engine block | 40 Nm +1/2 turn further (180º) | |
Engine console to body | 50 | |
Engine mount to engine console | 40 + 90° → Note → Note | |
Connection to engine console/body | 20 + 90° → Note → Note | |
Pendulum support to subframe | 100 + 90° → Note → Note | |
Front supercharger air tube to the engine block | 22 |
|