Fabia Mk1
![]()
|
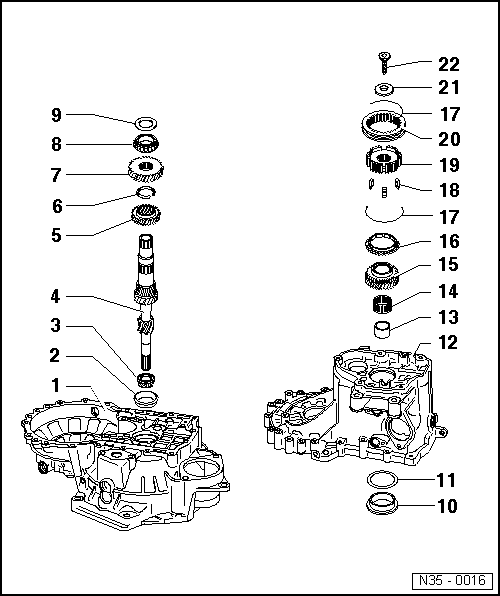
1 - | Clutch housing |
2 - | Outer ring/tapered-roller bearing |
q | pressing out → Fig. |
q | installing → Fig. |
3 - | Inner ring/tapered-roller bearing |
q | pressing off → Fig. |
q | installing → Fig. |
4 - | Drive shaft |
q | adjust → Chapter |
5 - | 3rd gear pinion |
q | Collar points to the 4th gear |
q | pressing off → Fig. |
q | pressing on → Fig. |
6 - | Circlip |
q | always replace → Electronic Catalogue of Original Parts |
7 - | 4th gear pinion |
q | pressing off with inner ring/tapered-roller bearing and bushing → Fig. |
q | pressing on → Fig. |
q | Collar points to the 3rd gear |
8 - | Inner ring/tapered-roller bearing |
q | press off with 4th gearwheel and bushing → Fig. |
q | pressing on → Fig. |
9 - | Thrust washer |
10 - | Outer ring/tapered-roller bearing |
q | pressing out → Fig. |
q | installing → Fig. |
11 - | Adjusting washer |
q | Determine thickness → Chapter |
12 - | Gearbox housing |
13 - | Bushing |
q | for needle bearing |
q | press off with 4th gearwheel and inner ring/tapered-roller bearing → Fig. |
q | pressing on → Fig. |
q | insert thrust washer Pos. 9 before assembly |
14 - | Needle bearing |
15 - | 5th gear sliding gear |
q | removing and installing → Chapter |
16 - | 5th gear synchronizer ring |
q | with integrated arresters → Chapter |
q | check for wear → Chapter |
17 - | Spring |
q | Fitting position → Fig. |
q | on gearboxes as of manufacturing date 10.04 the spring was changed → Fig. |
q | Fitting position → Fig. |
18 - | Arresters (3 pieces) |
q | Fitting position → Fig. |
q | on gearboxes as of manufacturing date 03.01 are installed the arresters, which are hollow inside |
19 - | 5th gear synchronizer body |
q | removing and installing → Chapter |
20 - | 5th gear sliding sleeve |
q | removing and installing → Chapter |
21 - | Disc spring |
q | Fitting position → Chapter |
22 - | 80 Nm |
q | holds disc spring in position with sleeve socket on screw head → Chapter |
q | always replace → Electronic Catalogue of Original Parts |
|
![]() |
|
![]() |
|
![]() |
|
![]() |
|
![]() |
|
![]() |
|
![]() |
|
![]() |
|
![]() |
|
![]() |
|
![]() |
|
![]() |
|
![]() |
|
![]() |
|
![]() |