Fabia Mk2

t | When installing new pinions or a new input shaft observe the technical data Fabia II → Chapter, Roomster → Chapter and Rapid → Chapter. |
t | Removing and installing output shaft → Chapter. |
t | Replace both tapered-roller bearings together. |
The output shaft can be disassembled as follows: |
– | Insert separating device under 2nd gear sliding gear Pos. 21 and press off as shown → Fig.. |
– | Remove circlip Pos. 17. |
– | Press off sliding sleeve with 1st and 2nd gear synchronizer body as shown in → Fig.. |
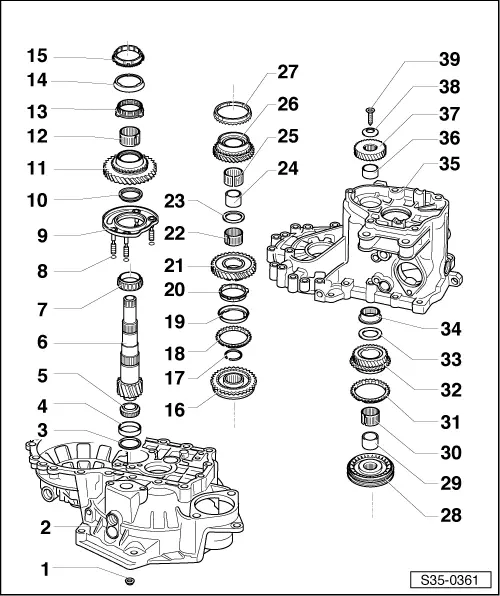
1 - | 25 Nm and torque a further 90° |
q | 4 nuts for bearing support Pos. 9 |
q | always replace → Electronic Catalogue of Original Parts |
2 - | Clutch housing |
3 - | Adjusting washer |
q | for output shaft |
q | Determine thickness → Chapter |
4 - | Outer ring/tapered-roller bearing small |
q | removing → Fig. |
q | pressing on → Fig. |
5 - | Inner ring/tapered-roller bearing small |
q | remove → Fig. |
q | pressing on → Fig. |
6 - | Output shaft |
q | adjust → Chapter |
7 - | Inner ring/tapered-roller bearing large |
q | remove → Fig. |
q | pressing on → Fig. |
8 - | O-ring |
q | Position O-rings (4 pieces) on the bearing support screws |
q | always replace → Electronic Catalogue of Original Parts |
9 - | Bearing support |
q | with outer ring/tapered-roller bearing large and with screws |
q | Always replace outer ring together with tapered-roller bearing large and bearing support |
10 - | Thrust washer |
q | Shoulder of thrust washer points to the tapered-roller bearing Pos. 7 |
11 - | 1st gear sliding gear |
12 - | Needle bearing |
q | for 1st gear |
13 - | Synchronizer ring |
q | (Inner ring for 1st gear) |
q | Fitting position → Fig. |
q | check for wear → Fig. |
q | Check pegs for traces of wear |
14 - | Outer ring for 1st gear |
q | place onto the inner ring Pos. 13 |
q | Fitting position → Fig. |
q | check for wear → Fig. |
q | replace if there are any traces of scoring or friction |
15 - | 1st gear synchronizer ring |
q | check for wear → Fig. |
q | Fitting position → Fig. |
16 - | Sliding sleeve with 1st and 2nd gear synchronizer body |
q | after removing the circlip Pos. 17 press off with bearing support Pos. 9 → Fig. |
q | disassembling → Fig. |
q | Assembling sliding sleeve/synchronizer body → Fig., → Fig. and → Fig. |
q | Fitting position → Fig. |
q | pressing on → Fig. |
17 - | Circlip |
18 - | 2nd gear synchronizer ring |
q | check for wear → Fig. |
q | insert in such a way that the recesses lock into the arresters of the sliding sleeve Pos. 16 |
19 - | Outer ring for 2nd gear |
q | insert into synchronizer ring Pos. 18 |
q | Fitting position → Fig. |
q | replace if there are any traces of scoring and friction → Electronic Catalogue of Original Parts |
20 - | Synchronizer ring |
q | (Inner ring for 2nd gear) |
q | check for wear → Fig. |
q | Check pegs for traces of wear |
q | Fitting position → Fig. |
21 - | 2nd gear sliding gear |
q | Fitting position → Fig. |
22 - | Needle bearing |
q | for 2nd gear |
23 - | Thrust washer |
24 - | Bushing |
q | for 3rd gear needle bearing |
q | press off with 2nd gear sliding gear → Fig. |
q | pressing on → Fig. |
25 - | Needle bearing |
q | for 3rd gear |
26 - | 3rd gear sliding gear |
27 - | 3rd gear synchronizer ring |
q | check for wear → Fig. |
28 - | Sliding sleeve with 3rd and 4th gear synchronizer body |
q | press off → Fig. together with 2nd gear Pos. 21 and and 3rd gear Pos. 26 sliding gear |
q | disassembling → Fig. |
q | Assembling sliding sleeve/synchronizer body → Fig., → Fig. and → Fig. |
q | Fitting position sliding sleeve/synchronizer body → Fig. |
q | pressing on → Fig. |
29 - | Bushing |
q | for 4th gear needle bearing |
q | press off together with sliding sleeve and 3rd and 4th gear synchronizer body Pos. 28 → Fig. |
q | pressing on → Fig. |
30 - | Needle bearing |
q | for 4th gear |
31 - | 4th gear synchronizer ring |
q | check for wear → Fig. |
32 - | 4th gear sliding gear |
33 - | Thrust washer |
34 - | Needle bearing |
q | for output shaft |
q | removing and installing → Chapter |
35 - | Gearbox housing |
36 - | Bushing |
q | for needle bearing/output shaft Pos. 34 |
q | pressing off → Fig. |
q | pressing on → Fig. |
37 - | 5th gear pinion |
q | remove separately → Chapter |
q | remove together with gearbox housing → Chapter |
q | installing → Chapter |
38 - | Disc spring |
q | Fitting position → Chapter |
39 - | 80 Nm and torque a further 90° |
q | holds disc spring in position with sleeve socket on screw head |
q | always replace → Electronic Catalogue of Original Parts |
|
![]() |
|
![]() |
|
![]() |
|
![]() |
![]()
|
![]() |
|
![]() |
|
![]() |
|
![]() |
![]()
|
![]() |
|
![]() |
Dimension „a“ | Fitting dimension | Wear limit |
1st and 2nd gear | 0.75 … 1.25 mm | 0.3 mm |
|
![]() |
Dimension „a“ | Fitting dimension | Wear limit |
1st and 2nd gear | 1.2 … 1.8 mm | 0.5 mm |
|
![]() |
|
![]() |
|
![]() |
|
![]() |
|
![]() |
|
![]() |
|
![]() |
|
![]() |
|
![]() |
|
![]() |
Dimension „a“ | Fitting dimension | Wear limit |
3rd and 4th gear | 1.0 … 1.7 mm | 0.5 mm |
|
![]() |
|
![]() |
|
![]() |
|
![]() |
|
![]() |
|
![]() |
|
![]() |