Superb
1) Adjustments need to be made when replacing these parts. Setting overview → Chapter. |
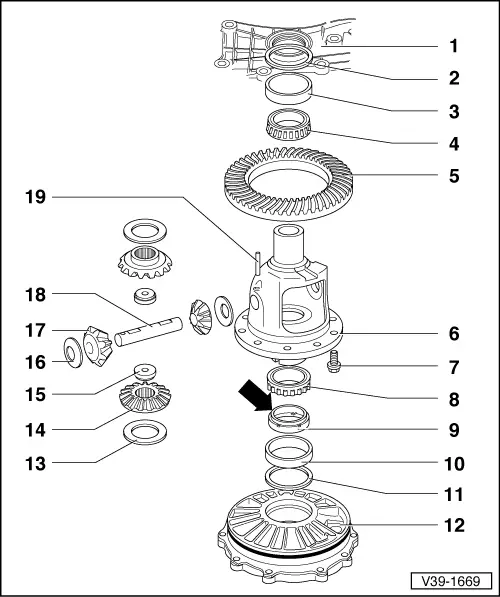
1 - | Gearbox housing1) |
2 - | Adjusting washer S2 |
q | Note thickness |
q | Setting overview → Chapter |
3 - | Outer ring/taper roller bearing, small1) |
q | extracting → Fig. |
q | inserting → Fig. |
4 - | Inner ring/taper roller bearing, small1) |
q | remove → Fig. |
q | pressing on → Fig. |
5 - | Crown wheel1) |
q | paired with secondary shaft (drive train) |
q | according to gearbox identification characters → Chapter assign via the → Electronic Catalogue of Original Parts. |
q | drive out with drift pin → Fig. |
q | mounting on differential housing → Fig. |
6 - | Differential1) |
7 - | 60 Nm and turn a further 45° |
q | always replace → Electronic Catalogue of Original Parts |
q | use original replacement parts only |
8 - | Inner ring/taper roller bearing, large1) |
q | remove → Fig. |
q | pressing on → Fig. |
9 - | Drive wheel for speedometer |
q | removing and installing → Chapter |
q | Fitting position: Collar -arrow- points towards differential gear; catch studs in recess of differential gear housing |
q | do not tilt |
10 - | Outer ring/taper roller bearing, large1) |
q | extracting → Fig. |
q | inserting → Fig. |
11 - | Adjusting washer S1 |
q | Note thickness |
q | Setting overview → Chapter |
12 - | Cover1) |
q | for final drive |
q | with O-ring seal |
q | Replace O-rings → Electronic Catalogue of Original Parts |
q | Lubricate O-ring seal when installing |
13 - | Adjusting washer |
q | Determining thickness again → Fig. |
14 - | Differential bevel gear large |
q | installing → Fig. |
q | adjust → Fig. |
15 - | Threaded part |
16 - | Thrust washer |
q | check for breaks or cracking |
17 - | Differential bevel gear small |
q | installing → Fig. |
q | adjust → Fig. |
18 - | Differential bevel gear shaft |
q | after removing tensioning pin Pos. 19, drive out with drift pin |
q | before inserting, align thrust washers |
19 - | Tensioning pin |
q | always replace → Electronic Catalogue of Original Parts |
q | insert flush |
|
![]() |
|
![]() |
|
![]() |
|
![]() |
|
![]() |
|
![]() |
|
![]() |
![]()
![]() |
![]() |
|
![]() |
Adjusting washer thickness (mm) | ||
0,50 | 0,70 | 0,90 |
0,60 | 0,80 | 1,00 |
|
![]() |
|
![]() |
|
![]() |
|
![]() |