Golf Mk3
Repairing drive shaft |
Drive shafts on vehicles with Plus running gear have shorter and finer splines on the outer joint. A 12-point nut is used to secure to wheel bearing. |
The splines of the outer joint and the wheel hub are bonded with locking fluid -D 185 400 A2-. |
Removing and installing drive shaft for vehicles with Plus running gear → Chapter. |

t | Quantity of grease for vehicles up to 48 kW: 90 g G 6.3 on outside and inside |
t | Quantity of grease for vehicles with 55 kW and above: |
t | Outside: 110 g G 6.3 |
t | Inside: 120 g G 6.3 |
t | Greasing outer joint: press half of the grease into the joint and the other half evenly into the bellows. |
t | Greasing inner joint: press half of the grease into the joint from both sides and the other half evenly into the bellows. |
t | Regrease joint if required when renewing boot. |
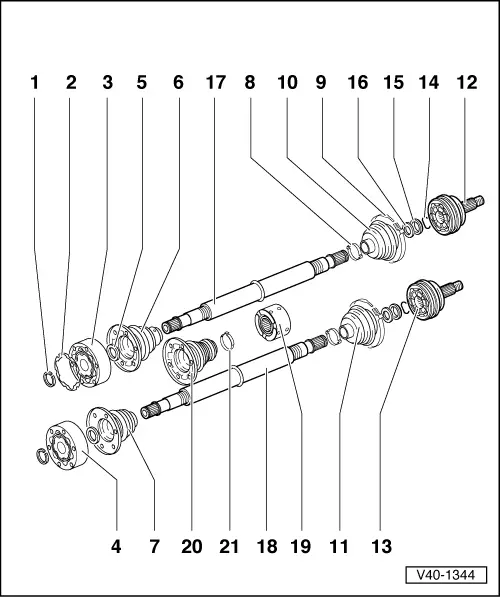
1 - | Retaining ring |
q | Renew |
q | Remove and install with circlip pliers -VW 161 A-. |
2 - | Gasket |
q | Renew: Pull off protective foil and stick onto joint. Only 100 mm Ø constant velocity joints. |
Modification |
q | As of 08.93 also on constant velocity joints with 90 mm Ø. |
3 - | Inner constant velocity joint 100 mm Ø for vehicles with output of 55 kW and above |
q | Renew only complete. |
q | Pressing off → Fig.. |
q | Pressing on → Fig.. |
q | Greasing → Chapter |
q | Checking → Chapter |
4 - | Inner constant velocity joint 94 mm Ø for vehicles with output up to 48 kW |
q | Pressing off → Fig.. |
q | Pressing on → Fig.. |
q | Greasing → Chapter |
q | Checking → Chapter |
5 - | Dished spring |
q | Splines in inner diameter. |
q | Installation position: larger Ø (concave side) contacts constant velocity joint. |
6 - | Joint protective boot for 100 mm Ø constant velocity joint |
q | With vent hole |
q | Check for splits and chafing. |
q | Installation position for left shaft → Fig. |
q | Installation position for right shaft → Fig.. |
q | Coat cap with D3. |
q | Drive off with drift. |
7 - | Joint protective boot for 94 mm Ø constant velocity joint |
q | Check for splits and chafing. |
q | Drive off with drift. |
8 - | Clamp |
q | Renew |
q | Tensioning → Fig. and → Fig.. |
9 - | Hose clip |
q | Renew |
q | Tensioning → Fig. and → Fig.. |
10 - | Joint protective boot for 90 mm Ø constant velocity joint |
q | Check for splits and chafing. |
q | Allow air to enter joint protective boot briefly to balance pressure before tightening small clamp in place → Fig.. |
11 - | Joint protective boot for 81 mm Ø constant velocity joint |
q | Check for splits and chafing. |
q | Allow air to enter joint protective boot briefly to balance pressure before tightening small clamp in place → Fig.. |
12 - | Outer constant velocity joint 90 mm Ø for vehicles with output of 55 kW and above |
q | Renew only complete. |
q | Removing → Fig. |
q | Installing: drive onto shaft with plastic hammer until compressed retaining ring seats. |
q | Greasing → Chapter |
q | Checking → Chapter |
13 - | Outer constant velocity joint 81 mm Ø for vehicles with output up to 48 kW |
q | Renew only complete. |
q | Removing → Fig. |
q | Installing: drive onto shaft with plastic hammer until compressed retaining ring seats. |
q | Greasing → Chapter |
q | Checking → Chapter |
14 - | Retaining ring |
q | Renew |
q | Insert in groove in shaft. |
15 - | Thrust washer |
16 - | Dished spring |
q | Outer Ø (concave side) contacts thrust washer. |
17 - | Drive shaft for vehicles with output of 55 kW and above |
q | Constant velocity joint splines 4 mm longer than shafts for lower-output engines, measured from dished spring support to retaining ring groove. |
18 - | Drive shaft for vehicles with output up to 48 kW |
19 - | Damper weight |
q | Installation position → Fig.. |
20 - | Constant velocity joint boot 94 and 100 mm Ø |
q | Fitted as of 01.93. |
21 - | Hose clip |
q | Tightening → Fig.. |
|
![]() |
Dimension “a” mm | Engine |
541 ± 1 | 1.8 l - 55 kW |
1.8 l - 66 kW | |
1.9 l - 48 kW | |
1.9 l - 55 kW | |
2.0 l - 85 kW | |
2.0 l - 110 kW | |
525 ± 1 | 1.9 l - 47 kW |
1.9 l - 66 kW |
|
![]() |
![]()
|
![]() |
![]()
|
![]() |
|
![]() |
|
![]() |
![]()
|
![]() |
|
![]() |