Golf Mk6
Removing and installing oil sump |
![]()
|
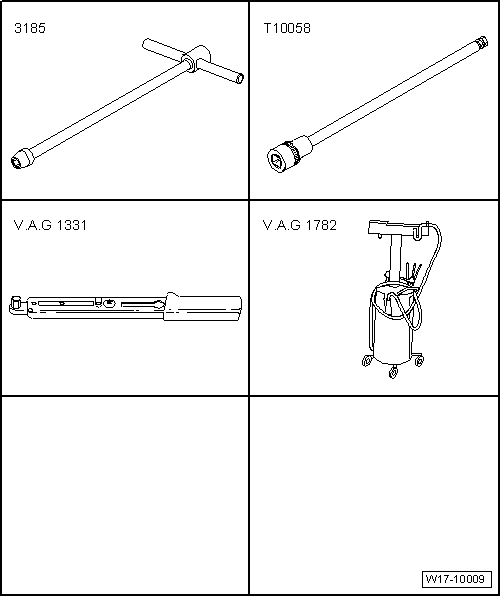
Special tools and workshop equipment required |
t | 10 mm jointed spanner -VAS 3185- |
t | Allen key, long reach -T10058- |
t | Torque wrench (5…50 Nm) -V.A.G 1331- |
t | Used oil collection and extraction unit -V.A.G 1782- |
![]()
|
|
![]() |
|
![]() |
|
![]() |
|
![]() |
![]()
|
![]() |
|
![]() |
![]()
![]()
![]()
|
![]() |