Passat (B3)
Repairing drive shaft |
Drive shafts on vehicles with Plus running gear have shorter and finer splines on the outer joint. A 12-point nut is used to secure to wheel bearing. |
The splines of the outer joint and the wheel hub are locked with locking compound -D 185 400 A2- on vehicles with Plus running gear. |
Removing and installing drive shaft: |
t | Vehicles with basic running gear → Chapter. |
t | Vehicles with Plus running gear → Chapter. |

t | Greasing: outer constant velocity joint 100 g G-6.3, inner constant velocity joint 110 g G-6.3 |
t | Greasing outer joint: press half of the grease into the joint and the other half evenly into the bellows. |
t | Greasing inner joint: press half of the grease into the joint from both sides and the other half evenly into the bellows. |
t | Regrease joint if required when renewing boot. |
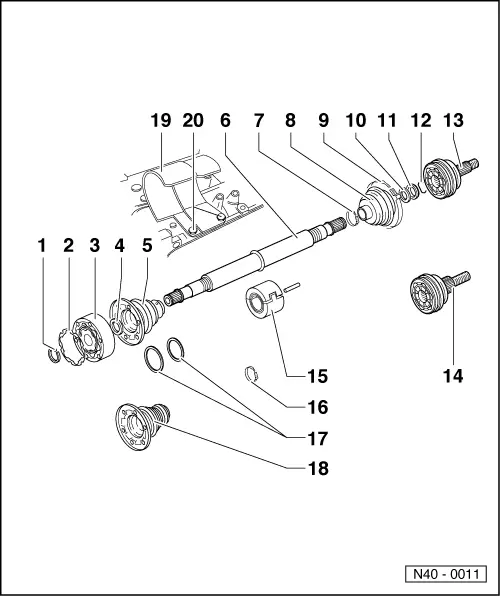
1 - | Circlip |
q | Renew. |
q | Remove and install with circlip pliers -VW 161 A-. |
2 - | Gasket |
q | Renew: Pull off protective foil and stick onto joint. Only 100 mm Ø constant velocity joints. |
3 - | Inner constant velocity joint, 100 mm Ø |
q | Renew only complete. |
q | Pressing off → Fig.. |
q | Pressing on → Fig.. |
q | Greasing → Chapter. |
q | Checking → Chapter. |
4 - | Dished spring |
q | Splined on internal Ø. |
q | Installation position: larger Ø (concave side) contacts constant velocity joint. |
5 - | Joint protective boot for 100 mm Ø constant velocity joint |
q | Rubber version. |
q | With vent hole. |
q | Check for splits and chafing. |
q | Installation position for left shaft → Fig.. |
q | Installation position for right shaft → Fig.. |
q | Coat cap with D3. |
q | Drive off with drift. |
6 - | Drive shaft |
q | Left full shaft (not illustrated). |
q | Right tubular shaft. |
7 - | Clamp |
q | Renew. |
q | Tensioning → Fig. and → Fig.. |
8 - | Joint protective boot for 90 mm Ø constant velocity joint |
q | Polyester elastomer version. |
q | Check for splits and chafing. |
q | Allow air to enter joint protective boot briefly to balance pressure before tightening small clamp in place → Fig.. |
q | Installation position for left shaft, wheel side → Fig. and → Fig.. |
q | Installation position for right shaft, wheel side → Fig.. |
9 - | Clamp |
q | Renew. |
q | Tensioning → Fig. and → Fig.. |
10 - | Dished spring |
q | Outer Ø (concave side) contacts thrust washer. |
11 - | Thrust washer |
12 - | Circlip |
q | Renew. |
q | Insert in groove in shaft. |
13 - | 90 mm Ø outer constant velocity joint |
q | Renew only complete. |
q | Removing → Fig.. |
q | Installing: drive onto shaft with plastic hammer until compressed retaining ring seats. |
q | Greasing → Chapter. |
q | Checking → Chapter. |
14 - | 90 mm Ø outer constant velocity joint |
q | For vehicles with 16V or VR6 engine. |
q | Larger diameter tapered splines. |
q | Renew only complete. |
q | Removing → Fig.. |
q | Installing: drive onto shaft with plastic hammer until compressed retaining ring seats. |
q | Greasing → Chapter. |
q | Checking → Chapter. |
15 - | Vibration damper |
q | Removing and installing → Fig.. |
q | Installation position → Fig.. |
q | Available as replacement part. |
q | Is only installed on right tubular drive shaft. Exception: vehicles with 85 kW engine and 02C manual gearbox, only installed on left solid drive shaft. |
16 - | Clamp |
q | Renew. |
q | Tensioning → Fig. and → Fig.. |
17 - | Support ring |
q | Only on rubber versions of joint protective boots. |
q | Only gearbox side → Electronic parts catalogue “ETKA”. |
18 - | Joint protective boot for 100 mm Ø constant velocity joint |
q | Polyester elastomer version. |
q | Check for splits and chafing. |
q | Allow air to enter joint protective boot briefly to balance pressure before tightening small clamp in place → Fig.. |
19 - | Protective cap |
20 - | Hexagon bolt, 35 Nm |
![]()
|
![]() |
|
![]() |
Dimension “a” = | 521 ± 1 mm right shaft | |
264 ± 1 mm left shaft (if vibration damper is fitted) |
|
![]() |
![]()
|
![]() |
![]()
|
![]() |
|
![]() |
|
![]() |
![]()
|
![]() |
|
![]() |
![]()
|
![]() |
|
![]() |
|
![]() |