A3 Mk1
Dismantling and assembling gearbox housing cover, gearbox housing, selector mechanism, input shaft, output shaft (pinion shaft), differential and selector forks |
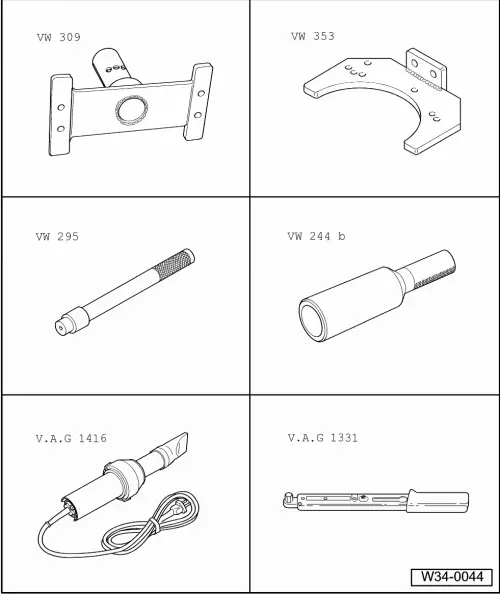
Special tools and workshop equipment required |
t | Support plate -VW 309- |
t | Gearbox support -VW 353- |
t | Drift -VW 295- |
t | Drift sleeve -VW 244 B- |
t | Hot air blower -V.A.G 1416- |
t | Torque wrench -V.A.G 1331- |

t | Hexagon key -V.A.G 1669- |
t | Used oil collection and extraction unit -V.A.G 1782- |
t | -1-Two-arm puller -Kukko 20/10- with hook -Matra V170- |
t | Stud M8x100 mm |
|
![]() |
![]()
|
![]() |
|
![]() |
![]()
|
![]() |
|
![]() |
|
![]() |
![]()
|
![]() |
|
![]() |
|
![]() |
|
![]() |
|
![]() |
|
![]() |
![]()
|
![]() |
![]()
|
![]() |
|
![]() |
![]()
|
![]() |
|
![]() |
![]()
|
![]() |
|
![]() |
|
![]() |
|
![]() |
|
![]() |
|
![]() |
|
![]() |
|
![]() |
|
![]() |
|
![]() |
|
![]() |
![]()
|
![]() |
|
![]() |
|
![]() |
![]() |
![]() |
![]()
|
![]() |
|
![]() |