Leon Mk1
Clutch housing: repairing |
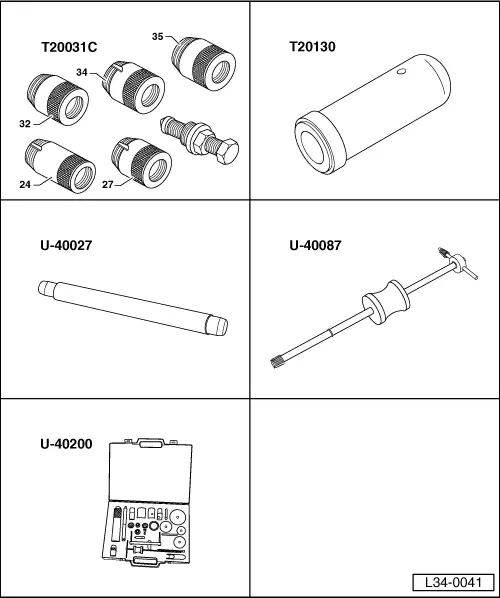
Special tools and workshop equipment required |
t | Oil seal extractor (Ø 24 mm) -T20031C- |
t | Oilseal fitting tool -T20130- |
t | Tool for fitting starter motor bush -U-40027- |
t | Threaded taps with hammer -U-40087- |
t | Gearbox repair set -U-40200- |
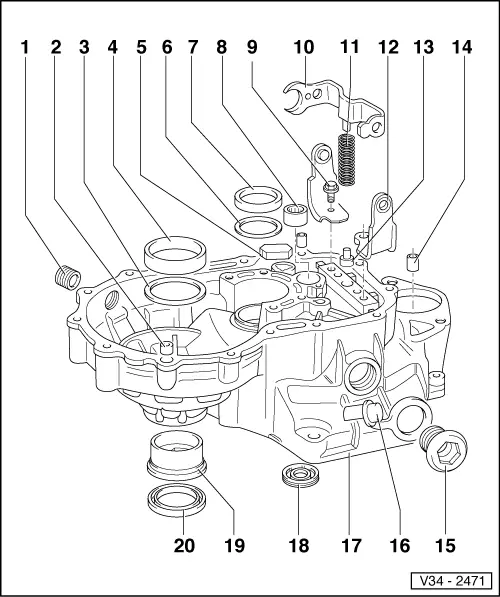
1 - | Oil drain screw |
q | 25 Nm |
q | Without magnet |
2 - | Adjustment sleeve |
q | 2 units |
3 - | Shim S2 |
q | Always 1 mm thick |
4 - | Outer track, roller bearing |
q | For differential |
q | Removing and fitting → Chapter |
q | If replaced, adjust differential → Chapter |
5 - | Magnet |
q | Secured between the gearbox casing and the clutch housing |
q | Assemble with sealing paste -AMV 188 200 03- |
6 - | Shim |
q | For layshaft |
q | Adjustment chart → Chapter |
7 - | Outer track, roller bearing |
q | For layshaft |
q | Removing and fitting → Chapter |
q | If replaced, adjust layshaft → Chapter |
8 - | Needle roller bearing |
q | For input shaft |
q | Remove → Fig. |
q | Fit → Fig. |
9 - | Hexagon bolt |
q | 25 Nm |
q | With locking teeth under the head |
10 - | Selection rod |
11 - | Spring |
12 - | Support for the coupling rod |
13 - | Runner |
14 - | Starter motor bush |
q | Remove → Fig. |
q | Fit → Fig. |
q | Can be replaced with the gearbox |
15 - | Plug |
q | Green: clutch diameter, 210 mm |
q | White: clutch diameter, 190 and 200 mm |

Always select the right bolt (e.g. when changing a gearbox or transforming a clutch). |
Consequences of fitting the wrong bolts: |
1. White bolt - |
210 mm Ø clutch |
– | The TDC sender would be destroyed and the flywheel markings damaged. Fragments of the sender would fall into the clutch housing. |
2. Green bolt - |
190 and 200 mm Ø clutch |
– | The checker would give no reading or and inexact or changing reading. |
16 - | Cover cap |
17 - | Clutch housing |
q | In case of replacement → Chapter, Adjustment chart |
18 - | Input shaft oilseal |
q | Remove → Fig. |
q | Fit → Fig. |
19 - | Bush |
q | For articulation flange oilseal, → Item |
q | Remove → Fig. |
q | Fit → Fig. |
20 - | Articulation flange oilseal |
q | Renew → Chapter, Articulation flange oilseals: removing and installing |
|
![]() |
|
![]() |
|
![]() |
|
![]() |
|
![]() |
|
![]() |
|
![]() |