Leon Mk1
Secondary shaft: dismounting and assembly |
t | If new pinions need to be fitted, consult the Identification Initials section, group assignment, reduction ratios, filling amounts → Chapter |
t | The secondary shaft must always be adjusted whenever components that may affect the position of the tapered roller bearings have been replaced. Consult the Adjustments chart → Chapter. |
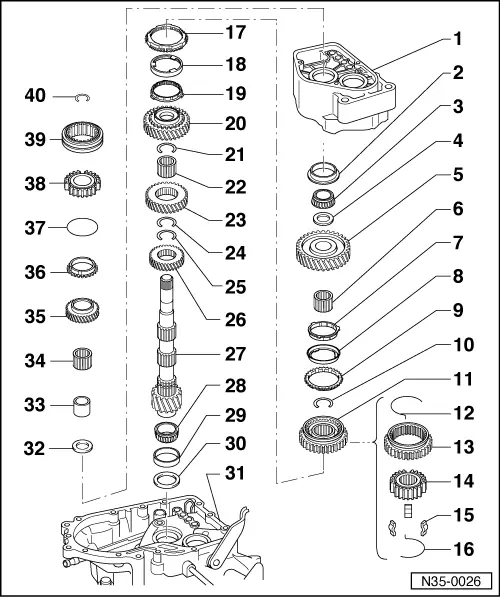
1 - | Gearbox casing |
2 - | Outer track, tapered roller bearing |
q | Detachment → Fig. |
q | Assembly → Fig. |
3 - | Tapered roller bearing |
q | Detach, together with the 1st gear pinion → Fig. |
q | Assembly: → Fig. |
4 - | Retainer washer |
5 - | 1st gear pinion |
q | Assembly position → Fig. |
6 - | Needle bearing for 1st gear pinion |
7 - | Inner synchroniser ring for 1st gear |
q | Checking for wear → Fig. |
q | Check that the flanges show no signs of wear. |
q | Assembly position → Fig. |
8 - | Outer ring for 1st gear |
q | Attach to the synchroniser ring for 1st gear → Item |
q | Assembly position → Fig. |
q | Replace if there are signs of wear or grooves |
9 - | 1st gear synchroniser ring |
q | Checking for wear → Fig. |
q | When assembling, the ring flanges must fit into the housings of the 1st and 2nd gear synchroniser unit → Item |
10 - | Guard ring |
q | Detachment → Fig. |
q | Attachment → Fig. |
11 - | Synchroniser unit for 1st and 2nd gears |
q | The parts go in pairs. |
q | Detachment → Fig. |
q | Component assembly → Fig. and → Fig. |
q | Assembly → Fig. |
12 - | Spring |
13 - | Sliding sleeve |
14 - | Synchroniser bush |
15 - | Cotters |
16 - | Spring |
17 - | 2nd gear synchroniser ring |
q | Checking for wear → Fig. |
q | Assembly position → Fig. |
18 - | Outer ring for 2nd gear |
q | Attach to the synchroniser ring → Item |
q | Assembly position → Fig. |
q | Replace if there are signs of wear or grooves. |
19 - | Inner synchroniser ring for 2nd gear |
q | Checking for wear → Fig. |
q | Check that there are no signs of wear on the flanges. |
q | Assembly position → Fig. |
20 - | 2nd gear pinion |
21 - | Guard ring |
q | Detachment → Fig. |
q | Attachment → Fig. |
22 - | Needle bearing for 2nd gear pinion |
23 - | 3rd gear pinion |
24 - | Guard ring |
q | Detachment → Fig. |
q | Attachment → Fig. |
25 - | Guard ring |
q | Detachment → Fig. |
q | Attachment → Fig. |
26 - | 4th gear pinion |
q | Assembly position: the identification notch must face the tapered unit. |
27 - | Secondary shaft |
q | If replacing, consult: Adjusting the secondary shaft → Chapter and the Identification Initials section, group assignment, reduction ratios, filling amounts → Chapter. |
28 - | Tapered roller bearing |
q | Removal → Fig. |
q | Attachment → Fig. |
29 - | Outer track, tapered roller bearing |
q | Removal → Fig. |
q | Attachment → Fig. |
30 - | Adjusting washer |
q | For the secondary shaft. |
q | Calculate the thickness → Chapter |
31 - | Clutch casing |
32 - | Retainer washer |
q | The washer step should end up facing the tapered roller bearing. |
33 - | Needle bearing bush |
q | Detachment → Anchor |
q | Assembly → Anchor |
34 - | Needle bearing for 5th gear pinion |
35 - | 5th gear pinion |
36 - | 5th gear synchroniser ring |
37 - | Spring |
q | Fit to the 5th gear synchroniser ring. |
q | Replace if it shows signs of wear. |
38 - | 5th gear synchroniser bush |
q | Detachment, assembly and adjustment → Chapter onwards |
39 - | Sliding sleeve |
q | Detachment, assembly and adjustment → Chapter onwards |
40 - | Guard ring |
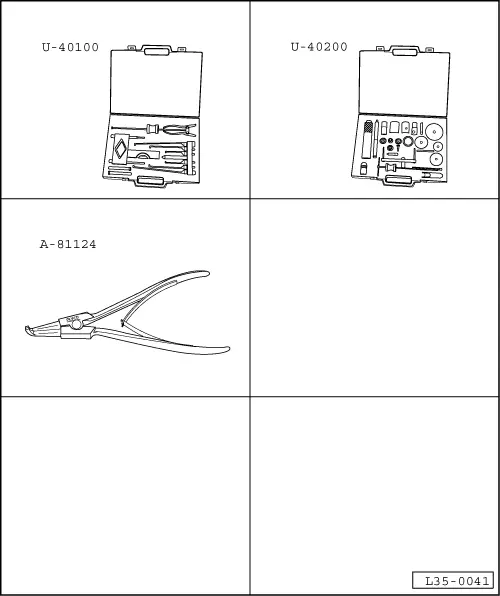
Special tools and workshop equipment required |
t | Case for extractor tools for gearboxes -U-40100- |
t | Replacement parts repair case -U-40200- |
t | Pliers for opening elastic rings -A-81124- |
|
![]() |
|
![]() |
|
![]() |
|
![]() |
|
![]() |
|
![]() |
|
![]() |
![]()
|
![]() |
|
![]() |
Synchroniser ring | Measurement “a” with the new synchroniser | Limit of wear |
1st and 2nd gear | 0,75…1,25 mm | 0,3 mm |
|
![]() |
Synchroniser ring | Measurement “a” with the new synchroniser | Limit of wear |
1st and 2nd gear | 1,2…1,8 mm | 0,5 mm |
|
![]() |
|
![]() |
|
![]() |
|
![]() |
|
![]() |
|
![]() |
|
![]() |
|
![]() |