Leon Mk1
Dismantling and assembling pistons and conrods |
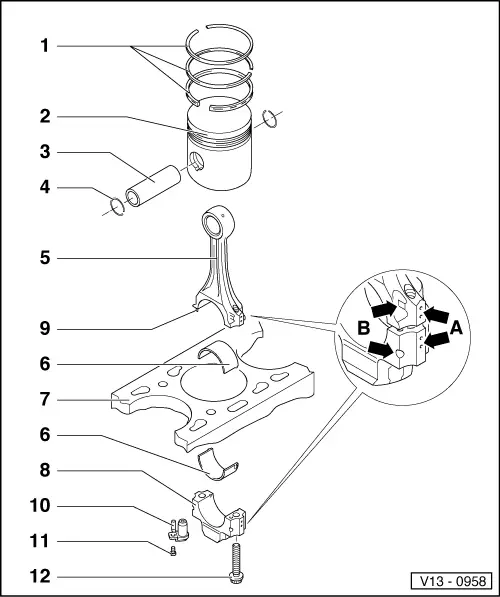
1 - | Piston rings |
q | Remove and install with piston ring pliers |
q | Offset gaps by 120° |
q | Check clearance |
q | “TOP” faces towards piston crown |
q | Checking ring gap → Fig. |
q | Checking ring to groove clearance → Fig. |
2 - | Piston |
q | Mark installation position and correspondence with the cylinder |
q | Installation position and piston/cylinder correspondence → Fig. |
q | Check piston position at TDC → Chapter |
q | Arrow on piston crown points to pulley end |
3 - | Piston pin |
q | Remove and install with -U-20008- tool |
q | Pin diameter = 26 mm |
4 - | Safety washer |
5 - | Conrod |
q | Only renew as a set |
q | Mark correspondence with cylinder number -A- |
q | The marks -B- must point to the distribution side |
q | Conrod length = 144 mm |
6 - | Conrod bearing shell |
q | Note the fitting position |
q | Do not interchange used bearing shells |
q | Make sure the retaining lugs are correctly seated. |
q | Axial clearance: Maximum: 0.37 mm |
q | Check radial clearance with Plastigage: Maximum: 0.08 mm |
q | Do not rotate the crankshaft when checking the radial clearance |
7 - | Cylinder block |
q | Checking cylinder bores → Fig. |
q | Piston and cylinder dimensions → Chapter. |
8 - | Conrod bearing cap |
q | The marks -B- must point to the distribution side |
9 - | Dowel peg |
q | They should house firmly in the bearing and not in the cap |
10 - | Oil injector |
q | For piston cooling |
11 - | 10 Nm |
q | Use suitable sealant for fitting |
12 - | 30 Nm + 1/4 turn (90°) |
q | Renew |
q | Oil the threads and contact surface |
q | To measure the radial clearance use an old bolt |
Gap | |||
Piston ring | New | Wear limit | |
1st compression ring | mm | 0.20 … 0.40 | 1.0 |
2nd compression ring | mm | 0.20 … 0.40 | 1.0 |
Oil scraper ring | mm | 0.25 … 0.50 | 1.0 |
|
![]() |
Clearance | |||
Piston ring | New | Wear limit | |
1st compression ring | mm | 0.06 … 0.09 | 0.25 |
2nd compression ring | mm | 0.05 … 0.08 | 0.25 |
Oil scraper ring | mm | 0.03 … 0.06 | 0.15 |
![]()
|
![]() |
![]()
|
![]() |