Fabia Mk1

t | Before installing heat the inner ring of the tapered-roller bearing to 100°C. |
t | Replace both tapered-roller bearings together. |
t | When replacing the tapered-roller bearing of the differential housing, gearbox housing and clutch housing adjust the differential → Chapter. |
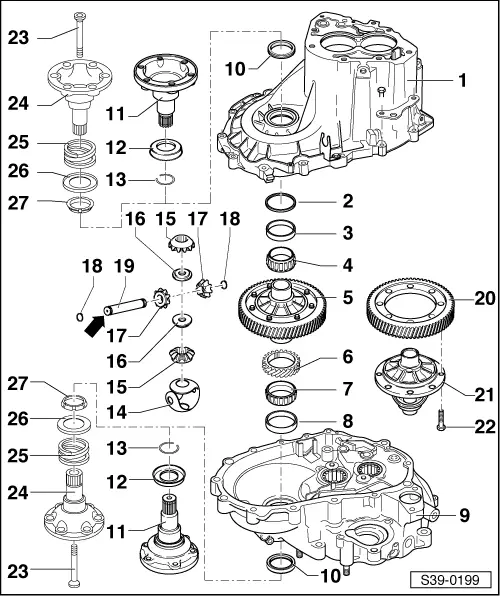
1 - | Gearbox housing |
2 - | Adjusting washer |
q | for the differential gear |
q | Determine thickness → Chapter |
3 - | Outer ring/tapered-roller bearing |
q | removing → Fig. |
q | pressing on → Fig. |
4 - | Inner ring/tapered-roller bearing |
q | remove → Fig. |
q | pressing on → Fig. |
5 - | Differential gear housing with pinion |
6 - | Drive wheel for speedometer |
q | only for vehicles without ABS; from 11.02 |
q | before pressing on the inner ring place it on the differential gear housing up to the stop |
7 - | Inner ring/tapered-roller bearing |
q | remove → Fig. |
q | pressing on → Fig. |
8 - | Outer ring/tapered-roller bearing |
q | removing → Fig. |
q | pressing on → Fig. |
9 - | Clutch housing |
10 - | Gasket ring |
q | replace → Chapter |
11 - | Flange shaft |
q | for gearbox up to 06.00 |
q | removing and installing → Chapter |
12 - | Dust cap |
q | for gearbox up to 06.00 |
q | for flange shaft |
q | remove → Fig. |
q | pressing on → Fig. |
13 - | Circlip |
q | for gearbox up to 06.00 |
q | always replace |
14 - | Stop disc compound |
q | when installing moisten with gearbox oil |
15 - | Differential bevel gear large |
q | pay attention to different versions |
q | Installation for gearbox up to 06.00 → Fig. |
q | Installation for gearbox after 06/00 → Fig. |
16 - | Threaded part |
q | for gearbox after 06.00 |
q | installing → Fig. |
17 - | Differential bevel gear small |
q | Installation for gearbox up to 06.00 → Fig. |
q | Installation for gearbox after 06/00 → Fig. |
18 - | Circlip |
q | always replace |
19 - | Differential bevel gear shaft |
q | Shaft has a different diameter, front side with centering hole -arrow- means a smaller diameter |
q | pressing out → Fig. |
q | pressing on → Fig. |
20 - | Pinion for final drive |
q | is paired with the output shaft, replace together |
21 - | Differential housing |
q | screw to pinion for final drive |
22 - | 80 Nm |
q | before tightening apply locking agent (e.g. -THREE BOND 1375 B-) |
23 - | Conical screw, 25 Nm |
q | for gearbox after 06.00 |
q | screw into threaded piece |
24 - | Flange shaft |
q | for gearbox after 06.00 |
25 - | Pressure spring for flange shaft |
q | for gearbox after 06.00 |
q | fitted behind flange shaft |
26 - | Thrust washer |
q | for gearbox after 06.00 |
q | Fitting position: Collar towards pressure spring |
27 - | Conical ring |
q | for gearbox after 06.00 |
q | Fitting position: Cone towards differential housing |
|
![]() |
|
![]() |
![]()
|
![]() |
![]()
|
![]() |
|
![]() |
![]()
|
![]() |
|
![]() |
|
![]() |
|
![]() |
|
![]() |
|
![]() |
|
![]() |