Yeti

t | When installing new pinions observe the technical data → Chapter. |
t | Insert all bearings, sliding gears and synchronizer rings onto the drive shaft with gear oil. |
t | Do not interchange the synchronizer rings, if re-used always assign to the original sliding gear. |
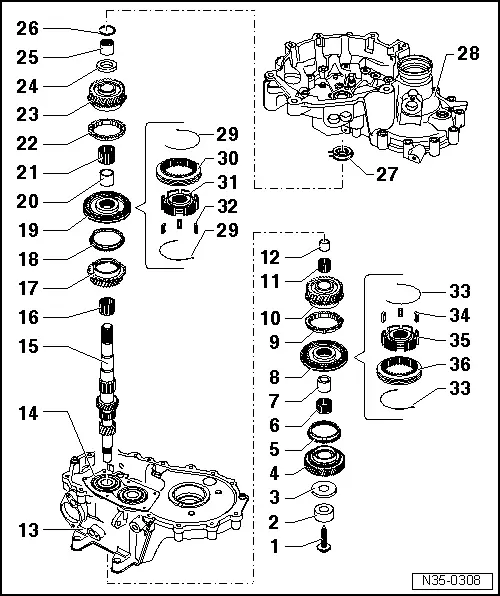
1 - | Screw |
q | removing and installing → Chapter |
2 - | Inner ring/cylindrical-roller bearing |
q | combined with thrust washer Pos. 3 on some gearboxes → Chapter |
q | identify before removing |
q | do not interchange with inner ring/cylindrical-roller bearing of output shaft |
q | can be replaced separately |
q | removing and installing → Chapter |
3 - | Thrust washer |
q | combined with inner ring/cylindrical-roller bearing Pos. 2 on some gearboxes → Chapter |
4 - | 6th gear sliding gear |
q | No. of teeth → Chapter |
5 - | 6th gear synchronizer ring |
q | check for wear → Fig. |
6 - | Needle bearing |
q | for 6th gear |
q | replace together with Pos. 7 |
q | on certain gearboxes two-piece, assign via the → Electronic Catalogue of Original Parts |
7 - | Bushing |
q | for 6th gear needle bearing |
q | replace together with Pos. 6 |
q | removing and installing → Chapter |
8 - | Sliding sleeve with 5th and 6th gear synchronizer body |
q | removing and installing → Chapter |
q | disassembling → Fig. |
q | Assembly of the sliding sleeve/5th/6th °gear synchronizer body → Fig. and → Fig. |
q | Fitting position → Fig. |
9 - | 5th gear synchronizer ring |
q | is damaged by the drive shaft when removing |
q | always replace → Electronic Catalogue of Original Parts |
q | check for wear → Fig. |
10 - | 5th gear sliding gear |
q | No. of teeth → Chapter |
11 - | Needle bearing |
q | for 5th gear |
q | replace together with Pos. 12 |
12 - | Bushing |
q | for 5th gear needle bearing |
q | replace together with Pos. 11 |
q | press off with bearing support/grooved ball bearing Pos. 14 |
q | pressing on → Fig. |
13 - | Gearbox housing |
q | repairing → Chapter |
14 - | Bearing support with grooved ball bearing |
q | Always replace grooved ball bearing together with the bearing support |
q | If the bearing support is released from the gearbox housing, it must always be replaced → Electronic Catalogue of Original Parts |
q | pressing off with 5th°gear pinion → Fig. |
q | pressing on → Fig. |
15 - | Drive shaft |
q | Clean the threaded hole in the drive shaft e.g with a thread tap from the locking agent residues |
16 - | Needle bearing |
q | for 3rd gear |
17 - | 3rd gear sliding gear |
q | No. of teeth → Chapter |
18 - | 3rd gear synchronizer ring |
q | check for wear → Fig. |
19 - | Sliding sleeve with 3rd and 4th gear synchronizer body |
q | press off with 3rd gear sliding gear → Fig. |
q | disassembling → Fig. |
q | Fitting position sliding sleeve/synchronizer body → Fig. |
q | assembling → Fig. |
q | pressing on → Fig. |
20 - | Bushing |
q | for 4th gear needle bearing |
q | replace together with Pos. 21 |
q | press off with 3rd gear sliding gear → Fig. |
q | pressing on → Fig. |
21 - | Needle bearing |
q | for 4th gear |
q | replace together with Pos. 20 |
22 - | 4th gear synchronizer ring |
q | check for wear → Fig. |
23 - | 4th gear sliding gear |
q | No. of teeth → Chapter |
24 - | Thrust washer |
25 - | Inner ring/cylindrical-roller bearing |
q | pressing off → Fig. |
q | pressing on → Fig. |
26 - | Circlip |
q | replace → Electronic Catalogue of Original Parts |
q | Determine thickness → Fig. |
27 - | Cylindrical-roller bearing |
q | with circlip |
q | removing → Fig. |
q | pressing on → Fig. |
q | Fitting position: the circlip in the bearing points towards the drive shaft |
28 - | Clutch housing |
q | repairing → Chapter |
29 - | Spring |
q | Fitting position → Fig. |
30 - | Sliding sleeve 3rd and 4th gear |
31 - | 3rd and 4th gear synchronizer body |
32 - | Arresters (3 pieces) |
33 - | Spring |
q | Fitting position → Fig. |
34 - | Arresters (3 pieces) |
35 - | Synchronizer body for 5th and 6th gear |
36 - | Sliding sleeve 5th and 6th gear |
|
![]() |
|
![]() |
![]()
|
![]() |
|
![]() |
|
![]() |
|
![]() |
|
![]() |
|
![]() |
Clearance -a- | Fitting dimension | Wear limit |
3., 4, 5 and 6th gear | 1,1 … 1.7 mm | 0.5 mm |
|
![]() |
|
![]() |
|
![]() |
![]()
|
![]() |
Measured value (mm) | Circlip thickness (mm) | Axial play (mm) |
0,05…0,14 | 2,0 | 0,05…0,15 |
0,15…0,24 | 2,1 | 0,05…0,15 |
0,25…0,34 | 2,2 | 0,05…0,15 |
0,35…0,44 | 2,3 | 0,05…0,15 |
0,45…0,51 | 2,4 | 0,05…0,10 |
![]() |
|
![]() |
|
![]() |
|
![]() |
|
![]() |
|
![]() |
|
![]() |