Fabia Mk1
![]()
|
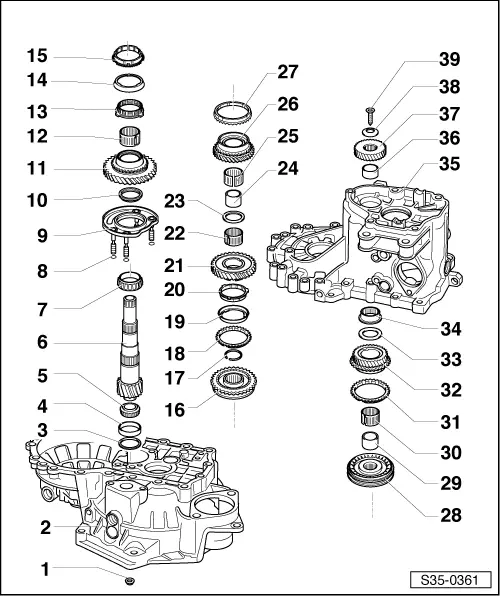
1 - | Nut, 25 Nm + 90° |
q | 4 nuts for bearing support |
2 - | Clutch housing |
3 - | Adjusting washer |
q | Determining thickness - Setting output shaft → Chapter |
4 - | Outer ring/tapered-roller bearing small |
q | removing → Fig. |
q | installing → Fig. |
5 - | Inner ring/tapered-roller bearing small |
q | remove → Fig. |
q | installing → Fig. |
6 - | Output shaft |
q | is paired with the gear pinion of the final drive, replace together |
q | adjust → Chapter |
7 - | Inner ring/tapered-roller bearing large |
q | remove → Fig. |
q | inserting → Fig. |
8 - | Gasket ring |
q | Insert gasket rings (4 pieces) on the bearing support screws |
9 - | Bearing support |
q | with outer ring/tapered-roller bearing large and with screws |
q | Always replace outer ring together with tapered-roller bearing large and bearing support |
10 - | Thrust washer |
q | Heel of thrust washer points to tapered-roller bearing |
11 - | 1st gear sliding gear |
12 - | Needle bearing |
q | for 1st gear |
13 - | Inner synchronizer ring for 1st gear |
q | check for wear → Fig. |
q | check lands for wear |
q | Fitting position → Fig. |
14 - | Outer ring for 1st gear |
q | place onto the inner ring Pos. 13, fitting position → Fig. |
q | replace if damaged or worn |
15 - | 1st gear synchronizer ring |
q | Identification → Fig. |
q | check for wear → Fig. |
q | Fitting position → Fig. |
16 - | Sliding sleeve with 1st and 2nd gear synchronizer body |
q | after removing the circlip Pos. 17 pull off above bearing support → Fig. |
q | disassembling → Fig. |
q | Assembling the sliding sleeve with synchronizer body → Fig. and → Fig. |
q | Fitting position → Fig. |
q | pressing on → Fig. |
17 - | Circlip |
18 - | 2nd gear synchronizer ring |
q | Identification → Fig. |
q | check for wear → Fig. |
q | insert in such a way that the recesses lock into the arresters on the sliding sleeve Pos. 16 |
19 - | Outer ring for 2nd gear |
q | insert into synchronizer ring Pos. 18, fitting position → Fig. |
q | replace if damaged or worn |
20 - | Inner synchronizer ring for 2nd gear |
q | check for wear → Fig. |
q | check lands for wear |
q | Fitting position → Fig. |
21 - | 2nd gear sliding gear |
q | Fitting position → Fig. |
22 - | Needle bearing |
q | for 2nd gear |
23 - | Thrust washer |
24 - | Bushing for 3rd gear needle bearing |
q | press off with 2nd gear sliding gear → Fig. |
q | pressing on → Fig. |
25 - | Needle bearing |
q | for 3rd gear |
26 - | 3rd gear sliding gear |
27 - | 3rd gear synchronizer ring |
q | check for wear → Fig. |
28 - | Sliding sleeve with 3rd and 4th gear synchronizer body |
q | press off → Fig. together with 2nd sliding gear Pos. 21 and 3rd gear Pos. 26 |
q | disassembling → Fig. |
q | Fitting position sliding sleeve with synchronizer body → Fig. |
q | Assembling the sliding sleeve with synchronizer body → Fig. and → Fig. |
q | pressing on → Fig. |
29 - | Bushing |
q | for needle bearing |
q | press off with sliding sleeve and 3rd and 4th gear synchronizer body Pos. 28 → Fig. |
q | pressing on → Fig. |
30 - | Needle bearing |
q | for 4th gear |
31 - | 4th gear synchronizer ring |
q | check for wear → Fig. |
32 - | 4th gear sliding gear |
33 - | Thrust washer |
34 - | Needle bearing |
q | for output shaft |
q | extracting → Fig. |
35 - | Gearbox housing |
36 - | Bushing |
q | for needle bearing of output shaft |
q | pressing off → Fig. |
q | pressing on → Fig. |
37 - | 5th gear sliding gear |
q | removing and installing → Chapter |
38 - | Disc spring |
q | Fitting position → Chapter |
39 - | 80 Nm |
q | holds disc spring in position with sleeve socket on screw head → Chapter |
q | always replace → Electronic Catalogue of Original Parts |
|
![]() |
|
![]() |
|
![]() |
|
![]() |
|
![]() |
|
![]() |
|
![]() |
|
![]() |
|
![]() |
Fitting dimension | Wear limit | |
Dimension -a- | 1.0 ... 1.7 mm | 0.5 mm |
|
![]() |
|
![]() |
|
![]() |
![]()
|
![]() |
|
![]() |
|
![]() |
Fitting dimension | Wear limit | |
Dimension -a- | 0.75 ... 1.25 mm | 0.3 mm |
|
![]() |
Fitting dimension | Wear limit | |
Dimension -a- | 1.2 ... 1.8 mm | 0.5 mm |
|
![]() |
|
![]() |
|
![]() |
|
![]() |
|
![]() |
|
![]() |
|
![]() |
|
![]() |
|
![]() |
|
![]() |
|
![]() |
|
![]() |
|
![]() |