Manual Gearbox 01E Drive Shaft Operation
![]()
|
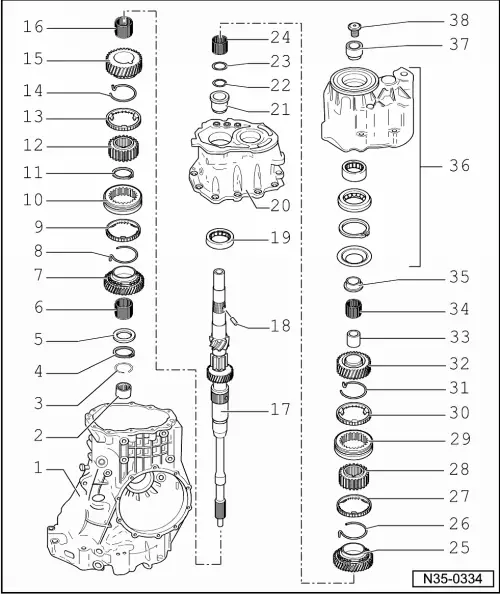
1 - | Gearbox housing |
q | repairing → Chapter |
2 - | Needle bushing |
q | for drive shaft |
q | extracting and driving in → Chapter |
3 - | Circlip |
q | for needle bushing |
4 - | Circlip |
q | for drive shaft |
5 - | Thrust washer |
6 - | Needle bearing |
q | for 4th gear |
q | identify before removing |
q | not to be confused with needle bearing for 3rd gear |
q | lubricate with gear oil before installing |
7 - | 4th gear sliding gear |
8 - | Spring |
q | place in the 4th gear sliding gear Pos. 7 → Fig. |
q | Assignment to sliding gear → Electronic Catalogue of Original Parts |
9 - | 4th gear synchronizer ring |
q | check for wear → Fig. |
10 - | Sliding sleeve 3rd and 4th gear |
q | is paired with synchronizer body Pos. 12 |
q | identify before removing → Chapter |
11 - | Circlip |
q | If replacing the synchronizer body Pos. 12, determine thickness of circlip again → Fig. |
q | Fitting position: ends in line with groove in synchronizer body |
12 - | Synchronizer body for 3rd and 4th gear |
q | pressing off → Fig. |
q | Fitting position → Fig. |
q | pressing on → Fig. |
13 - | 3rd gear synchronizer ring |
q | coated with molybdenum |
q | check for wear → Fig. |
14 - | Spring |
q | insert in the 3rd gear sliding gear Pos. 15 → Fig. |
q | Assignment to sliding gear → Electronic Catalogue of Original Parts |
15 - | 3rd gear sliding gear |
16 - | Needle bearing |
q | for 3rd gear |
q | identify before removing |
q | not to be confused with needle bearing for 4th gear |
q | lubricate with gear oil before installing |
17 - | Drive shaft |
18 - | Tensioning sleeve |
q | always replace → Electronic Catalogue of Original Parts |
q | insert when replacing the drive shaft → Fig. |
19 - | Cylindrical-roller bearing |
q | for drive shaft |
q | pressing in and pressing out → Chapter |
20 - | Bearing shield |
q | repairing → Chapter |
21 - | Inner ring |
q | for cylindrical-roller bearing |
q | position/remove manually |
22 - | Circlip |
23 - | Thrust washer |
q | for needle bearing for 6th gear sliding gear |
q | Fitting position: Collar for circlip, smooth thrust surface for needle bearing → Chapter |
24 - | Needle bearing |
q | for 6th gear |
q | lubricate with gear oil before installing |
25 - | 6th gear sliding gear |
q | after installing, check axial play with feeler gauge (0.15...0.35 mm) |
26 - | Spring |
q | insert in the 6th gear sliding gear Pos. 25 → Fig. |
q | Assignment to sliding gear → Electronic Catalogue of Original Parts |
27 - | 6th gear synchronizer ring |
q | check for wear → Fig. |
28 - | Synchronizer body for 5th and 6th gear |
q | xtracting and inserting → Chapter |
q | Fitting position: projecting hub towards 5th gear sliding gear |
29 - | Sliding sleeve 5th and 6th gear |
q | is paired with synchronizer body Pos. 28 |
q | identify before removing → Chapter |
30 - | 5th gear synchronizer ring |
q | check for wear → Fig. |
31 - | Spring |
q | insert in the 5th gear sliding gear Pos. 32 → Fig. |
q | Assignment to sliding gear → Electronic Catalogue of Original Parts |
32 - | 5th gear sliding gear |
33 - | Inner ring for needle bearing |
q | for 5th gear sliding gear |
q | xtracting and inserting → Chapter |
34 - | Needle bearing |
q | for 5th gear |
q | lubricate with gear oil before installing |
35 - | 1st Inner ring for four-point bearing |
q | Ball bearing side |
q | xtracting and inserting → Chapter |
36 - | Cover |
q | repairing → Chapter |
37 - | 2nd inner ring for four-point bearing |
q | Roller bearing side |
q | xtracting and inserting → Chapter |
38 - | Splined nut, 150 Nm |
q | slacken and tighten → Chapter |
|
![]() |
![]()
|
![]() |
Circlip thickness (mm) | ||
1,90 | 1,96 | 2,02 |
1,93 | 1,99 | 2,05 |
|
![]() |
|
![]() |
|
![]() |
|
![]() |